Delco-Remy in WWII
Delco-Remy WWII Marine
Equipment
Delco-Remy WWII Tank Products
Delco-Remy WWII Vehicle Products
Delco-Remy and LST-393
Delco-Remy WWII Kings Mills Plant
Delco-Remy WWII Antioch Foundry
Delco-Remy WWII
Stationary Engine Products
Delco-Remy WWII
Electrical Components for the Reo and Federal Truck, 20-Ton, 6x4
Delco-Remy Training Manuals for Aircraft Components
Delco-Remy in
World War Two
World War Two
Products and Product Applications
Aircraft Components for Military Aircraft
This page updated
5-5-2022.
The B-29 Project: Delco-Remy was
one of seventeen GM Divisions that built components for the B-29.
It
was the most expensive project of WWII, being even more expensive than
the Manhattan Project.
No mention of the B-29 is made in the 1944
Delco-Remy booklet "Our War Job". There are two reasons for this.
First, production on the B-29 did not start until mid-1944, and contracts
and tooling were still being made when the booklet was published.
Second, the B-29 project was considered "Top Secret." Delco-Remy
would have only been able to state it was working on the project, but
not what it was making for it. As diverse of an aircraft related
product line produced by DR during WWII, the Division could have
supplied any number of components for the B-29.
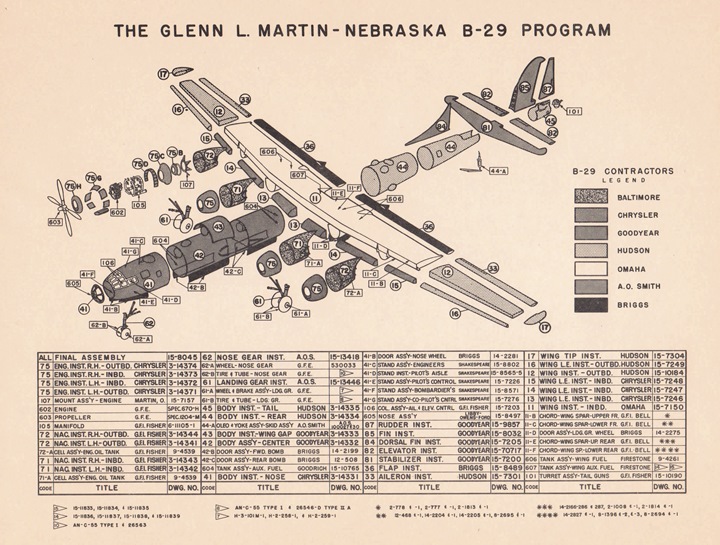
This Glenn Martin Company document shows the
major airframe suppliers for its plant in Omaha, NE.
Starting at the front of
the fuselage and working towards the rear of the aircraft, the glass
nose section was built by Libby-Owens-Ford, an automotive glass company.
The fuselage nose section was built by Chrysler's Plymouth
Division in Detroit. Goodyear in Akron, OH built the two bomb bay
fuselage sections. Briggs, an independent auto body manufacturer in
Detroit, provided the bomb bay doors. The three rear fuselage sections
behind the wings were also built in the city of Detroit by the Hudson
Motor Car Company, which combined with Nash in 1954 to become American
Motors. The entire tail section and the elevators with control surfaces
were made by Goodyear, and the tail gunner's position was manufactured by
the Fisher Body Division of GM at Cleveland, OH.
Martin Omaha provided the center section
of the wing. Chrysler provided the inboard leading edges.
Hudson built the outer wing sections, outer leading edges, ailerons, and
wing tips. Briggs provided the flaps.
All four engine nacelles and engine oil tanks came from the Fisher Body
Division of GM along with the exhaust manifolds. Omaha built the
engine mounts; Dodge supplied the engines and Chrysler the
engine cowlings.
Firestone provided the
main and auxiliary wing fuel tanks and BF Goodrich the fuselage
auxiliary fuel tank.
While Boeing
designed the aircraft, there are no major fuselage, wing nor rear tail
section components provided by that company. With the exception of the
Martin wing center section, the rest of the wing was supplied by the
American automobile industry.
Inside the B-29 airframe
and wing structural components listed above, there were tens of
thousands of parts and components. The engine nacelles produced by
the Fisher Body Division of GM had over 3,000 parts in them. Each
nose fuselage section built by Chrysler had 5,000 parts in it.
Many of the parts for many of the major components would have been
supplied by AC Sparkplug, Allison, Brown-Lipe-Chapin, Buick, Chevrolet,
Delco Appliance, Delco Products, Delco Radio, Delco-Remy, Fisher Body,
Frigidaire, Harrison Radiator, Hyatt Bearings, Moraine Products, New
Departure, Packard Electric, and Rochester Products Divisions of GM as
identified in the 1944 GM Annual Report.
Of significance is that
the Martin Plant in Omaha, NE produced the Silverplate B-29 Nuclear
Bombers.
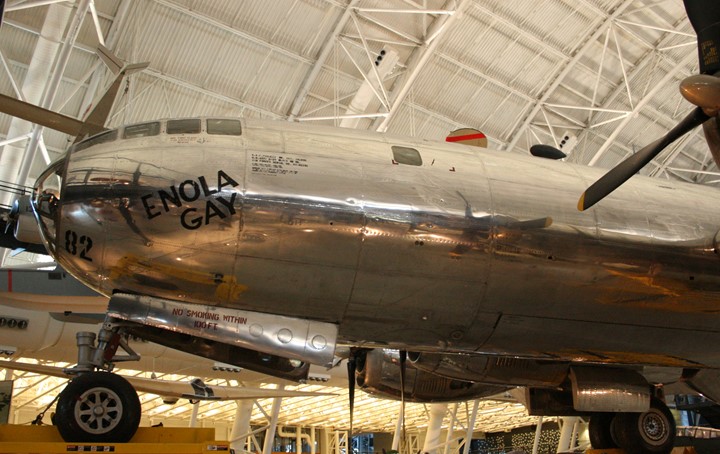
No doubt, some Delco-Remy component
went on a ride to Hiroshima, Japan in the Enola Gay on August 6, 1945.
Author's photo.
Delco-Remy Aircraft Equipment in World War
Two: Various models of aircraft
generators up to 6KW, aircraft regulators, aircraft magnetos, aircraft batteries,
automatic aircraft engine controls, and both solenoid valves and servos for the
Sperry Automatic Pilot.
Army Air Forces and Navy Aircraft utilizing
Delco-Remy Electrical Equipment in World War Two: Any of
the described aircraft equipment could be on any of the aircraft listed
below. It could have been one part or any number on the aircraft.
The World War Two military aircraft with Delco-Remy components included but was not limited to: C-47,
P-51, B-26, B-24, B-26, B-17, B-29, P-39, P-63, SBD, A-20, P-38, C-46, P-47,
PV-1
Automatic Pressure Regulator for Allison
V-1710 V-12 Aircraft Engine: This device maintains, within
desirable limits, a selected manifold pressure from sea level up to the
critical altitude of the supercharger. The selected sea level
manifold pressure is maintained up to the critical altitude without any
throttle adjustment. A drop of 1.5 Hg a the critical altitude is
built into the regulator to keep the engine from producing excessive
power during a climb when the manifold pressure is kept constant.
This automatic pressure regulator was build in
Plant Six and is on display at the Air Zoo Aviation Museum in Portage,
MI. The Allison V-1710 engine it is attached to is located in the
museum annex building. The regulator is serial number 15181 and is
an AAF Type A2 regulator.
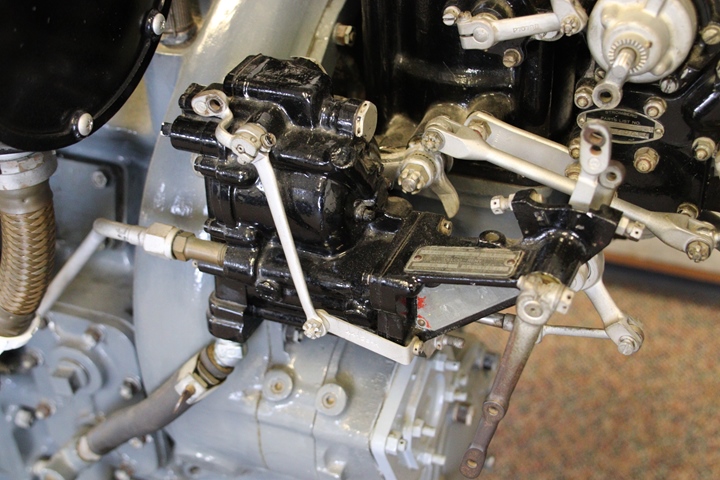
Author's photo added 2-1-2021.
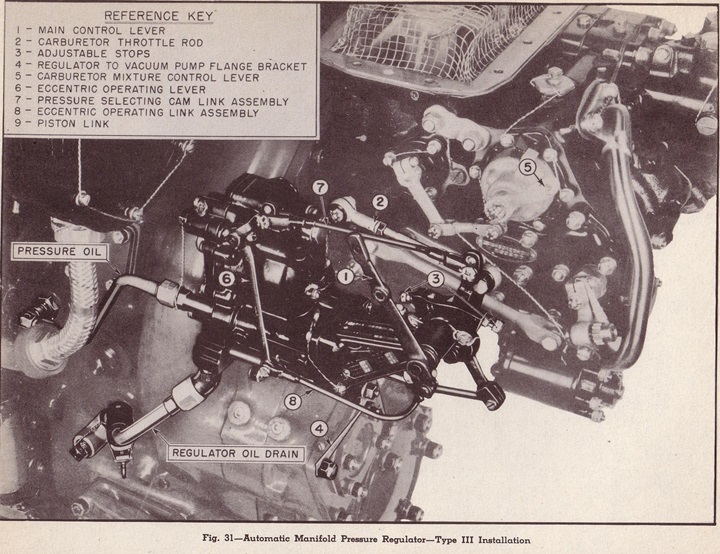
Image added 2-1-2021.
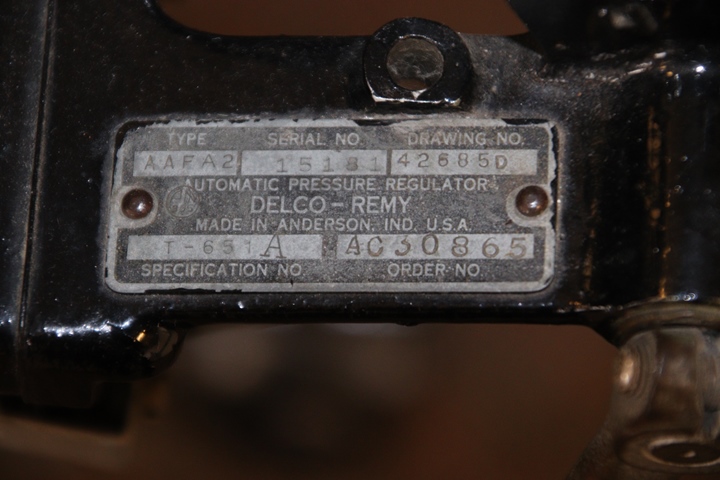
Author's photo added 2-1-2021.
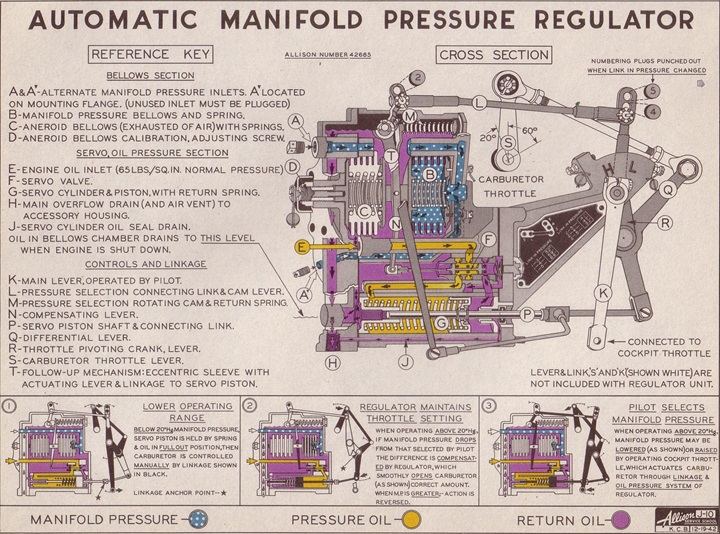
According to information on page 39 of "Our
War Job," there were 101 operations involved in machining the casting to
proper tolerances. Image added 2-1-2021.
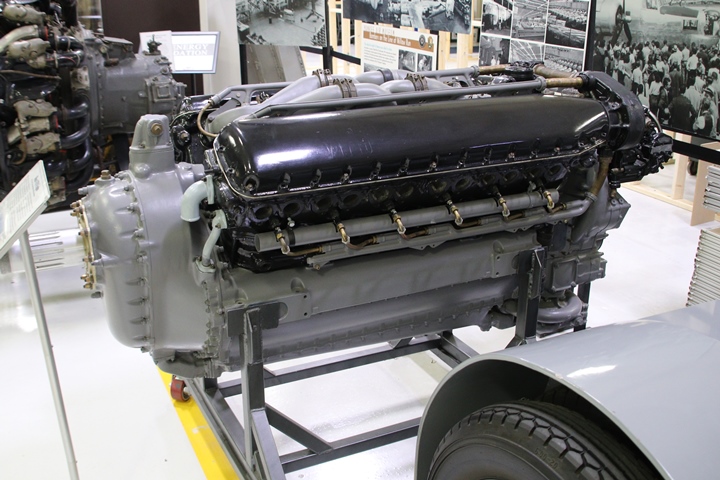
116 miles to the east of the Air Zoo is the
Yankee Air Museum in Bellevue, MI. This museum also has a Allison
V-1760 engine with a Delco-Remy automatic pressure regulator on it.
Authors' photo added 5-5-2022.
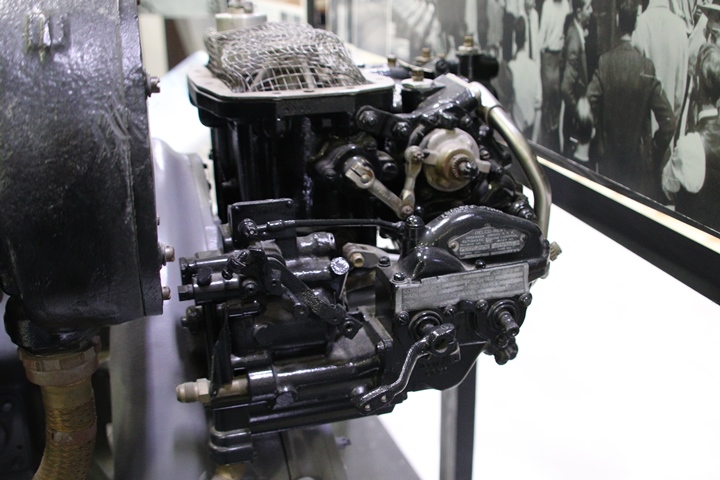
This is of a different design.
Authors' photo added 5-5-2022.
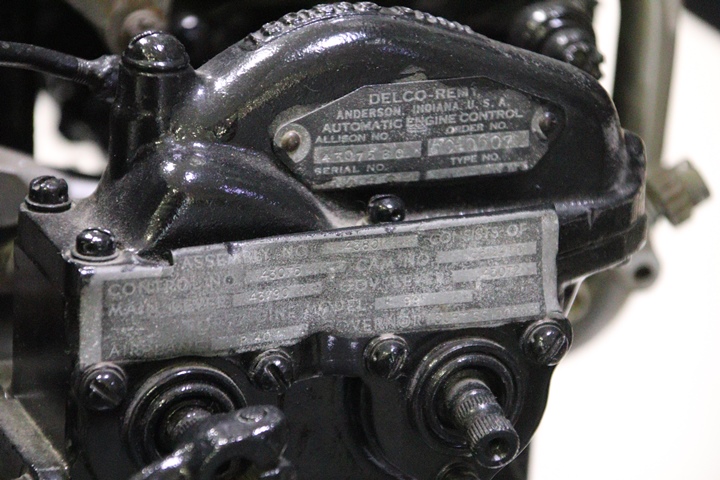
The serial number and type number are not
readable on the unit. Authors' photo added 5-5-2022.
Aircraft DC Generator: Sometimes
Delco-Remy World War Two products are hiding in plain sight. Many
times I have stopped and looked and photographed the Allison V-1710-85
engine display near the P-39Q at the National Museum of the Air Force.
On my visit of 9-9-2020 I decided to photograph the accessory
section of the engine, and discovered it had a Delco-Remy DC aircraft
generator. In the past, I had been more interested in the engine
itself and possible D-R castings on it, and not the accessories.
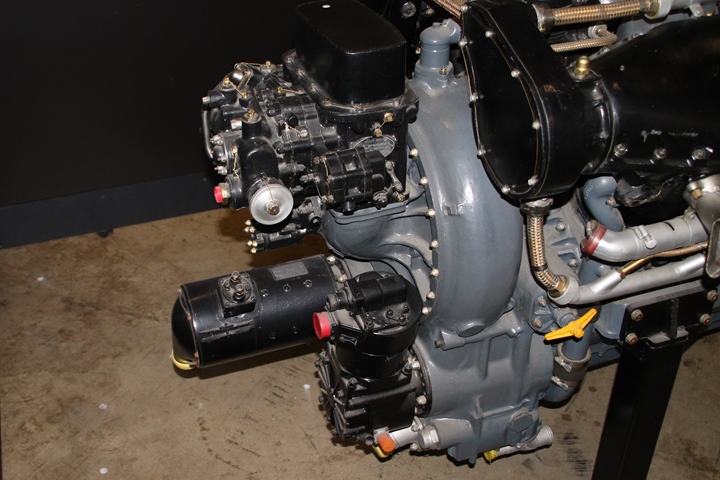
Author's photo added 9-15-2020.
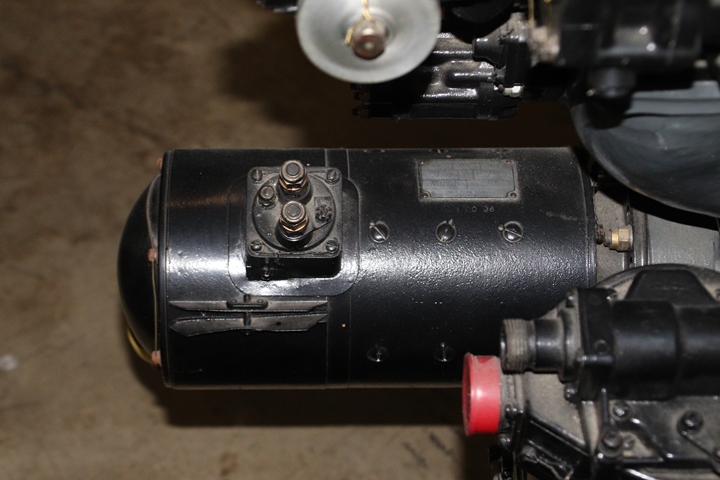
Author's photo added 9-15-2020.
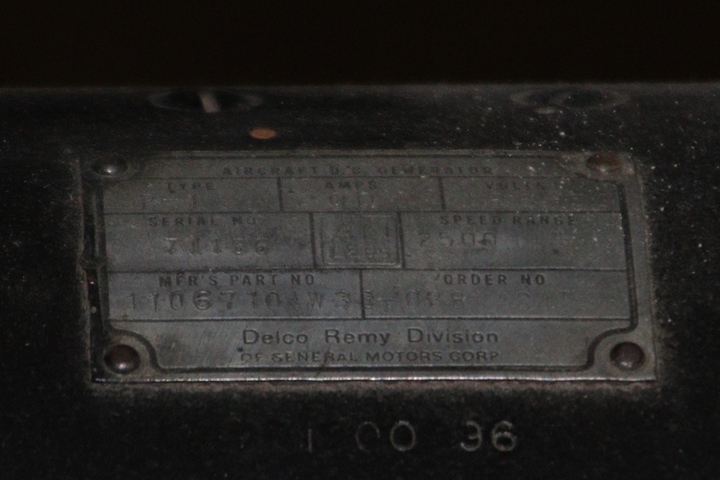
This is Delco-Remy part number 1106770.
Author's photo added 9-15-2020.
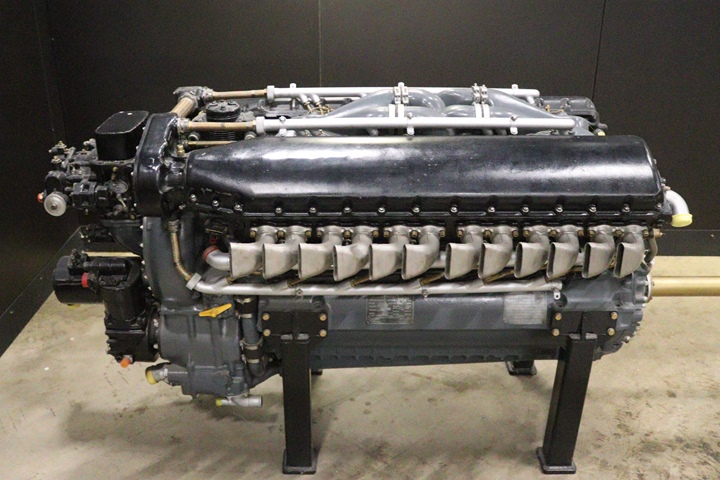
The Allison V-1710-85. Author's photo
added 9-15-2020.
Sperry Auto Pilot: Delco-Remy
supplied solenoids for aircraft autopilots during WWII.
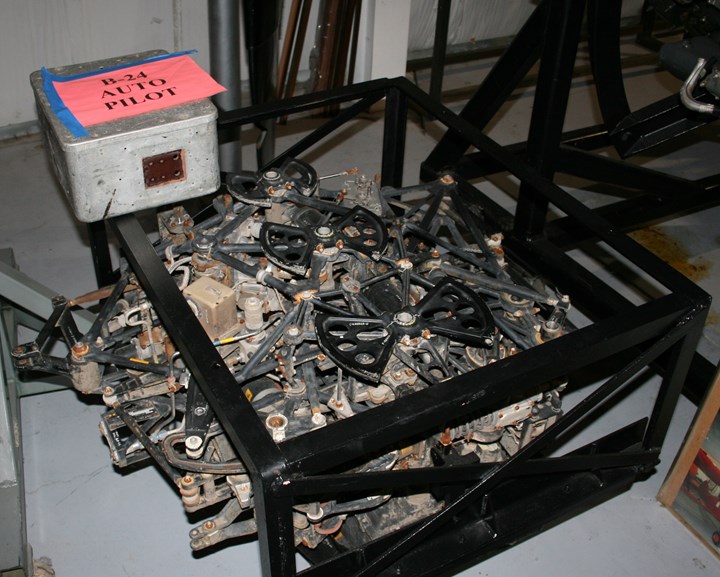
A B-24 auto pilot on display at the Hoosier
Air Museum in Auburn, IN. D-R solenoids are within this device.
Author's Photo.
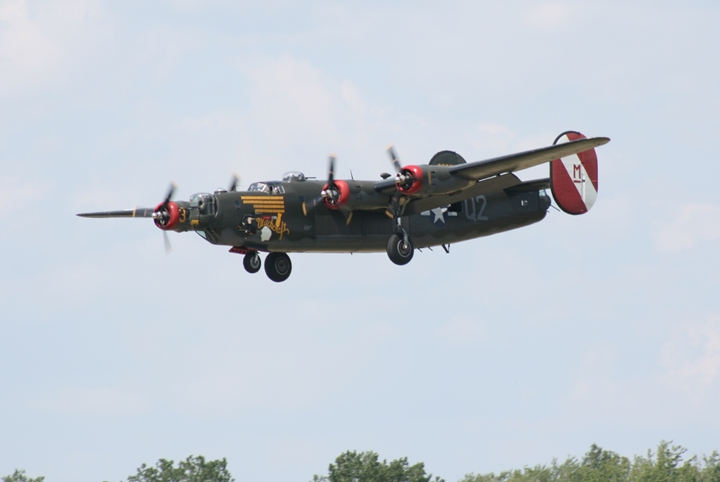
"Witchcraft" on final approach.
It is one of two B-24s still flying
today and is similar to B-24s that had Delco-Remy produced auto pilots. Author's Photo.
Aircraft Generator Carbon Pile Voltage
Regulator: Delco-Remy developed a carbon pile type aircraft
regulator that did not generate any electrical or radio interference
like the more common point contact regulator did. It was so
successful that the Army Air Force requested that Delco-Remy license
other manufacturers to build it for the war effort. Delco-Remy had
the best design for this device.
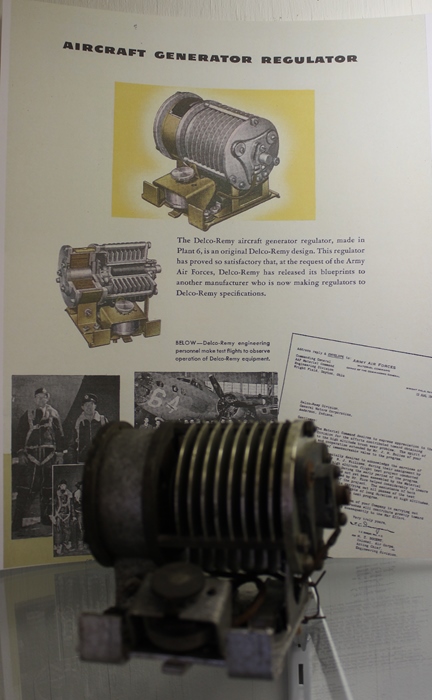
This aircraft voltage regulator was
featured at the 2016 Delco-Remy Exhibit at the Madison County Historical
Society. Author's photo added 5-16-2020.
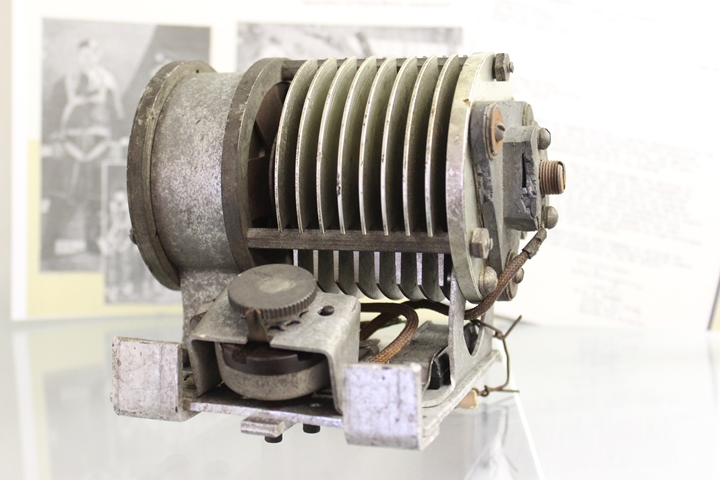
Author's photo added 5-16-2020.
Packard-built Rolls-Royce V-1650 Aircraft
Engine: According to the March 9,
1945 edition of the 'Delco-Remy Clan,' the Bedford, IN foundry had received new contracts
for increasing production on the Rolls-Royce aircraft engine. This
implies that Bedford had already been producing casting for the Packard-built Rolls-Royce V-1650 Merlin engine. This is the only reference
I have ever seen that Delco-Remy was supplying castings to any other
aircraft engine manufacturer besides Allison. The Packard-built
Merlin engine was the most important and best inline engine used in an Army Air
Force fighter during World War Two. It made the P-51 Mustang into
the best Army World War Two fighter aircraft.
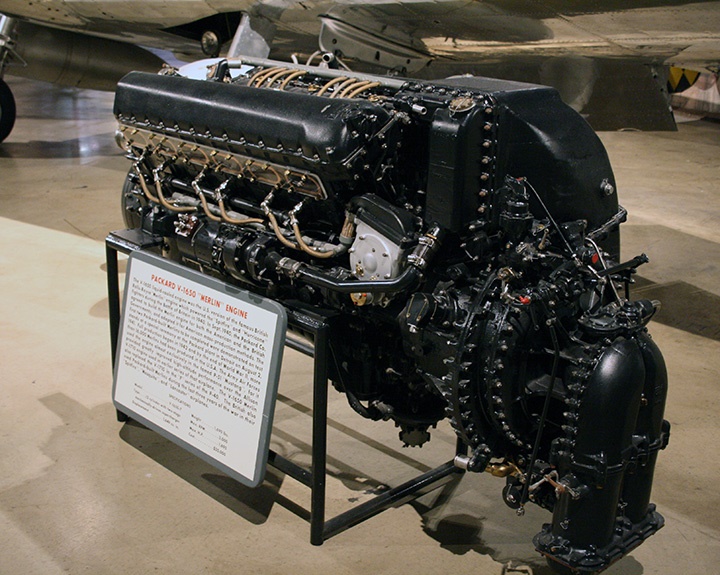
The Packard-built Rolls-Royce V-1650
Aircraft Engine. Author's photo added 5-16-2020.
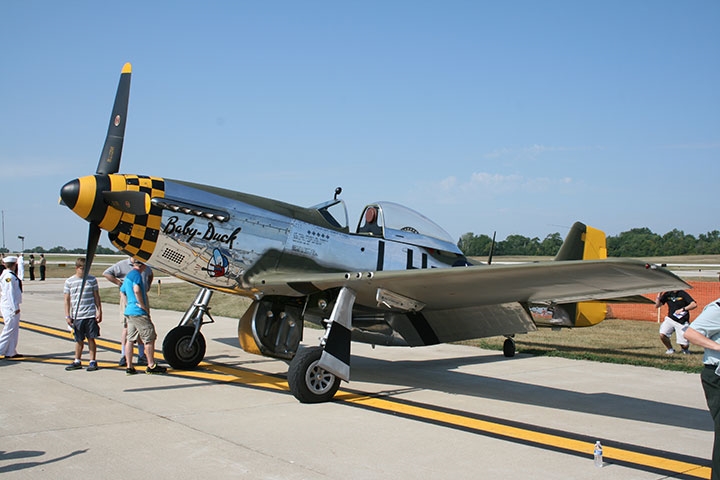
The P-51 Mustang with the Packard built
Merlin engine. The mating of the Merlin engine to the Mustang airframe
produced what is considered to be the best U.S. Army Air Force fighter
of World War Two. Author's photo added 5-16-2020.
The Allison V-1710 Aircraft
Engine:
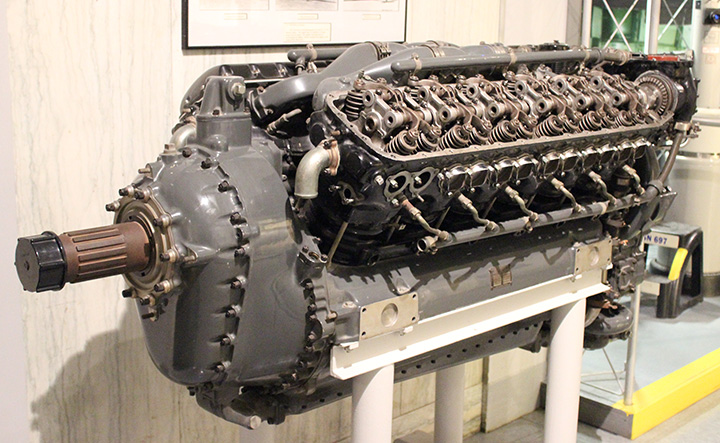
This Allison V-1710 is on display at the Indiana War Memorial in
downtown Indianapolis. The two nose housing castings and the intake
manifolds on top of the engine were produced in DR Plant 7. The
same can be said for the heads that are painted black and the gray engine block
below it. The valve cover that has been removed but is just
visible on the opposite side was also a Delco-Remy casting. Many
of the internal castings not visible here were also produced in Plant 7 and then
machined in Plant 10. Author's photo.
The photos below show aircraft that were
powered by the Allison V-1710 engine which had Delco-Remy castings.
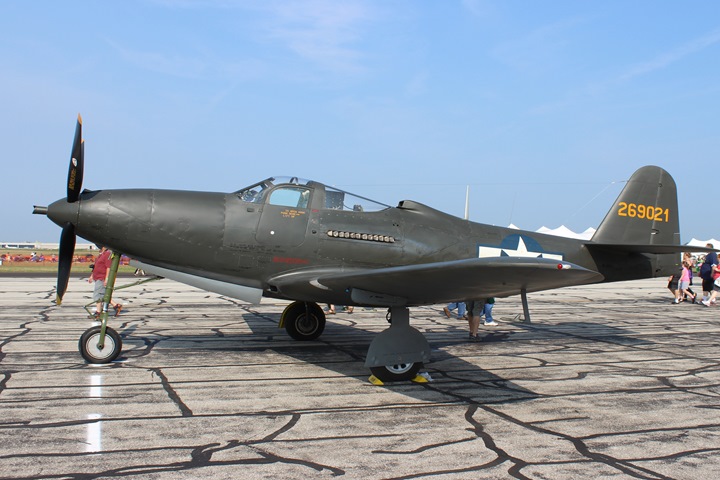
The Bell P-63. Author's photo.
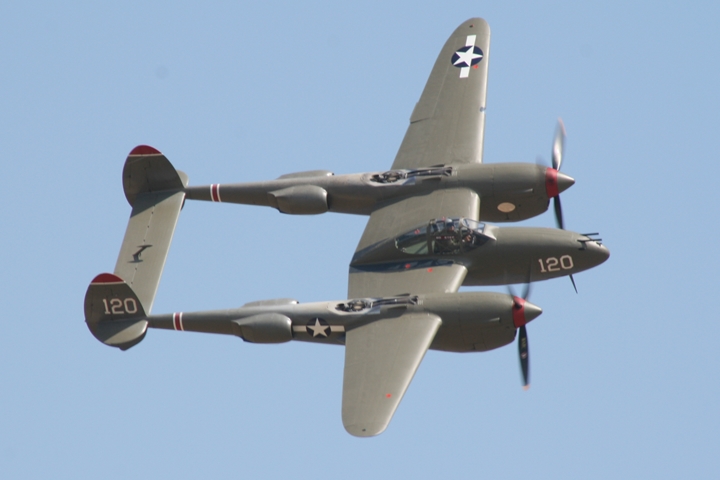
The Lockheed P-38L. Author's
photo.
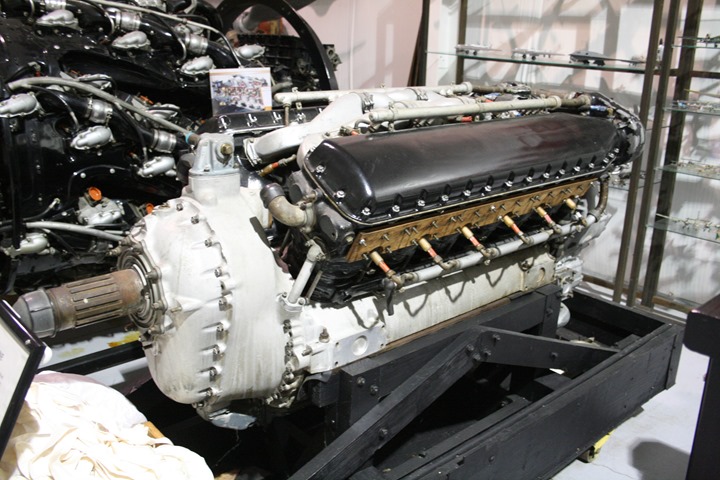
This Allison V-1710-69 aircraft engine with
Delco-Remy Plant 7 castings was used on the right engine of P-38L's like
the one shown above. Author's photo from the Hoosier Air Museum.
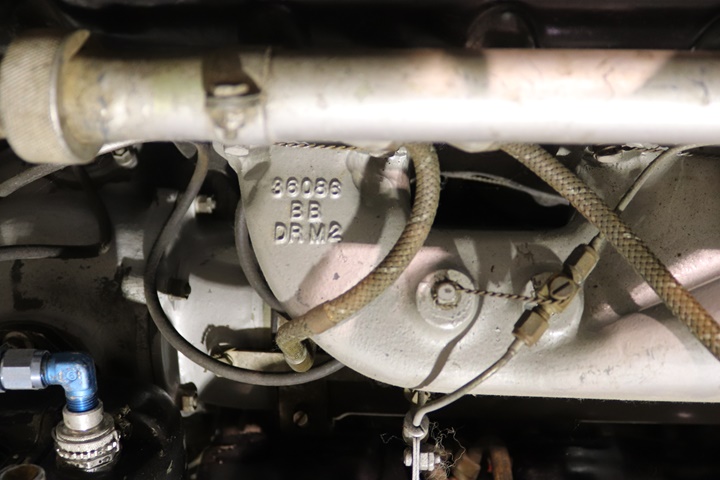
This intake manifold was cast on mold 2.
Author's photo from the Hoosier Air Museum.
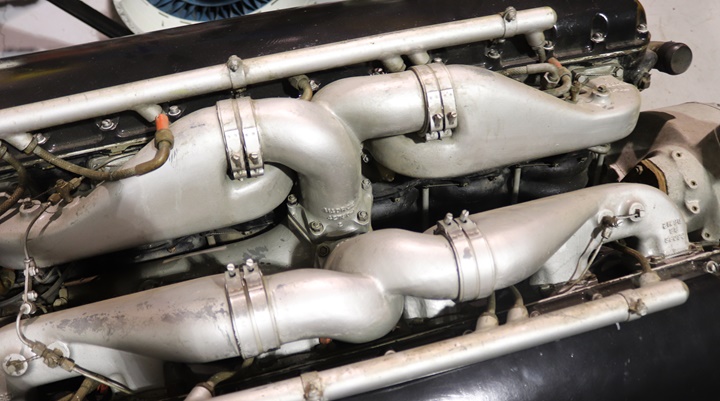
The top manifold was made on DR mold 4.
The bottom one, as noted above, was cast on mold 2. Author's
photo from the Hoosier Air Museum.
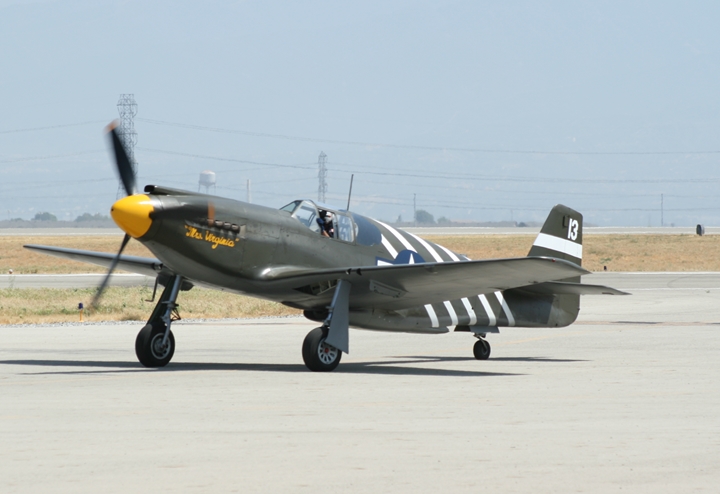
The North American P-51A.
Author's photo.
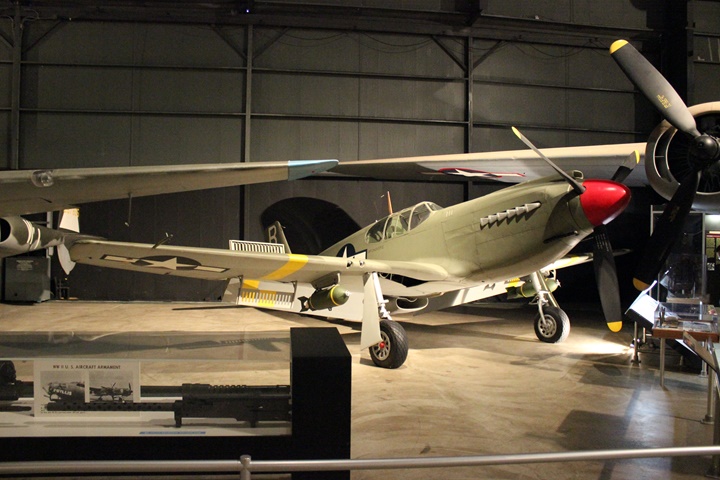
The North American A-36. Author's photo.
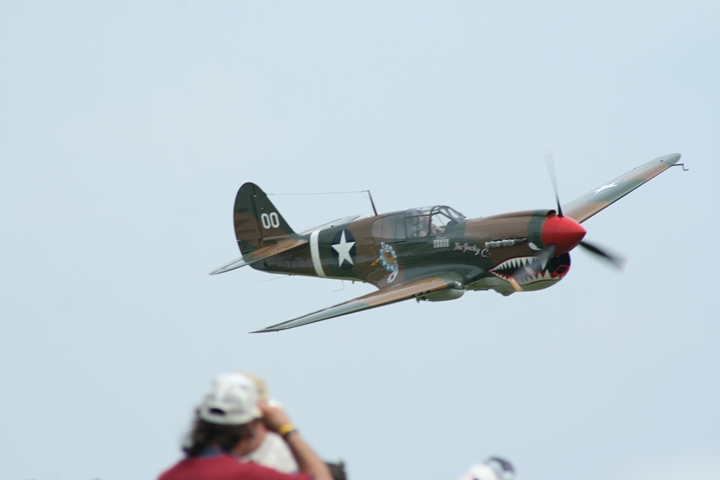
The Curtiss P-40. Author's
photo.
The Delco-Remy-built American Bosch Aircraft
Magneto: Delco-Remy
became a licensed supplier of American Bosch aircraft magnetos for the
Army Air Force during World War Two. In July 1942, initial contact
was made between the two companies that resulted in Delco-Remy building
more than 295,000 magnetos for the war effort. By April 1943,
Delco-Remy was running 15,000 magnetos a month in Plant 10. The
coils were built in Plant 1 and the molded parts in Plant 2. By
early 1943, known Delco-Remy Bosch magneto customers were
Chevrolet, Studebaker, and Jacobs. All built aircraft engines
during World War Two.
I have looked at a considerable number of
aircraft engines in many aviation museums attempting to find an example of
Delco-Remy Bosch type magneto. I finally found two of them on a Sunday
afternoon as I was visiting the Waco Museum in Troy, OH. The
engine was all the way in the back corner of the museum's second display building. There were two 1943 Delco-Remy magnetos on a Pratt
& Whitney 985 Wasp Junior engine.
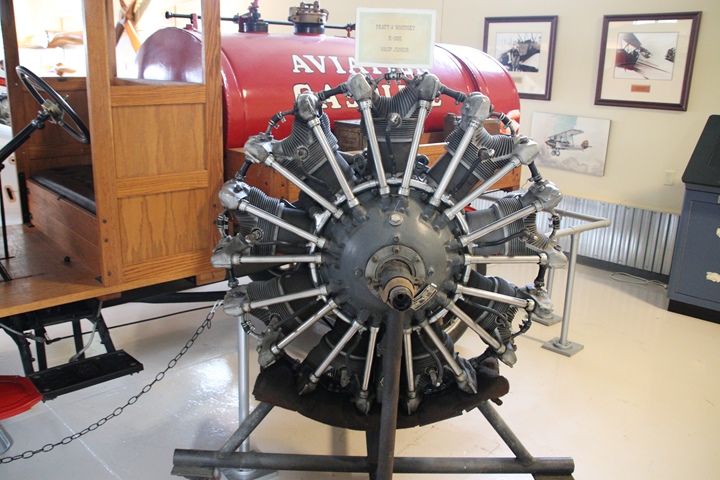
This is the Pratt & Whitney 985 Wasp Junior engine
at the Waco Museum. The engine was used on the BT-13 Valiant and
OS2U Kingfisher during World War Two. Author's photo added
9-15-2020.
Many display engines at museums do not have a complete set of
accessories mounted on them. Some have none, and just show the
front of the engine. In this case, both magnetos of Delco-Remy
manufacture were on the engine, while the carburetor, generator, and
starter were missing. Author's photo added 9-15-2020.
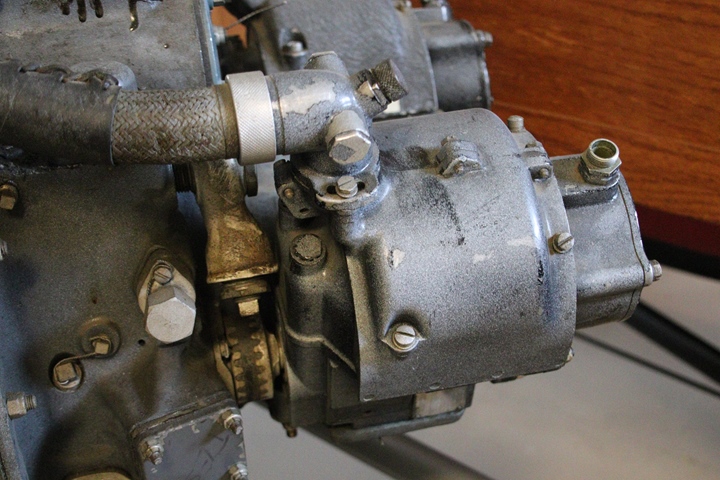
Author's photo added 9-15-2020.
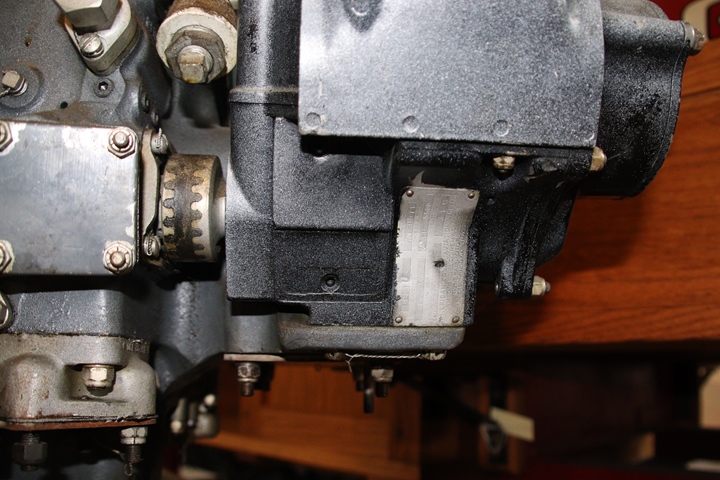
Author's photo added 9-15-2020.
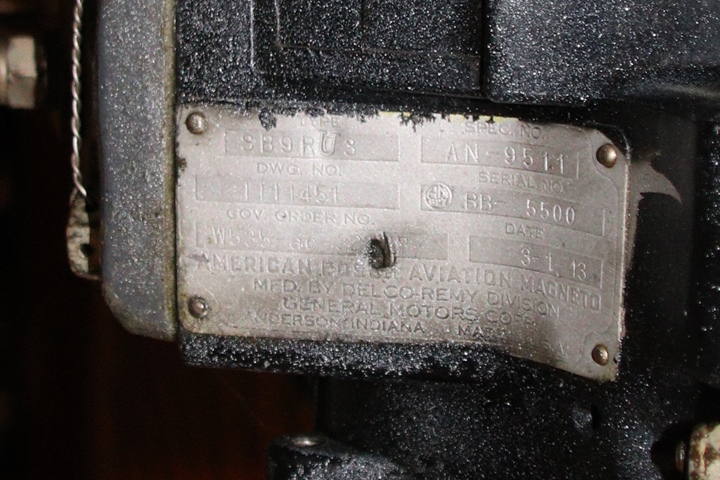
This is Delco-Remy Part Number 1111451 and
is Serial Number BB-5500. It was built on 3-1-1943. Author's
photo added 9-15-2020.
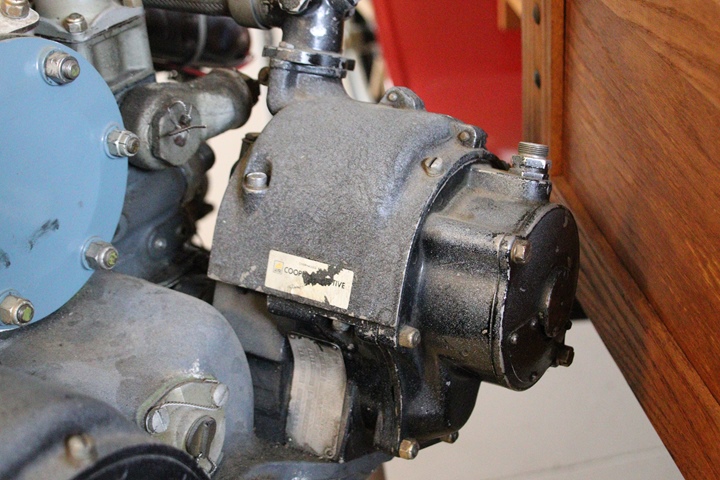
The second magneto was rebuilt by Cooper
Automotive, indicating the magneto was used on this engine after World
War Two. Author's photo added 9-15-2020.
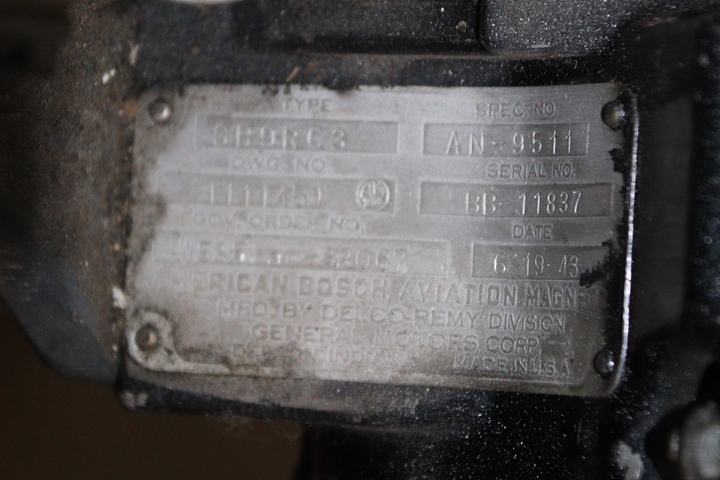
The magneto is Serial Number BB-11837 and
built on 6-19-1943. This indicates that Delco-Remy Plant 10 built
6,337 of this model in just over 3.5 months. It was one of five
models being produced at the time by Delco-Remy. Author's photo added 9-15-2020.
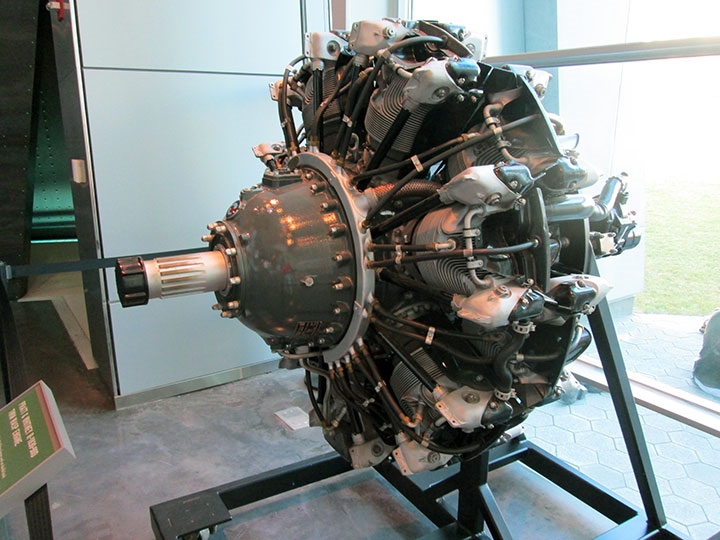
Chevrolet built the Pratt & Whitney R-1830
under license during World War Two and Delco-Remy supplied magnetos to
Chevrolet for this type of engine. Author's photo added
5-16-2020.
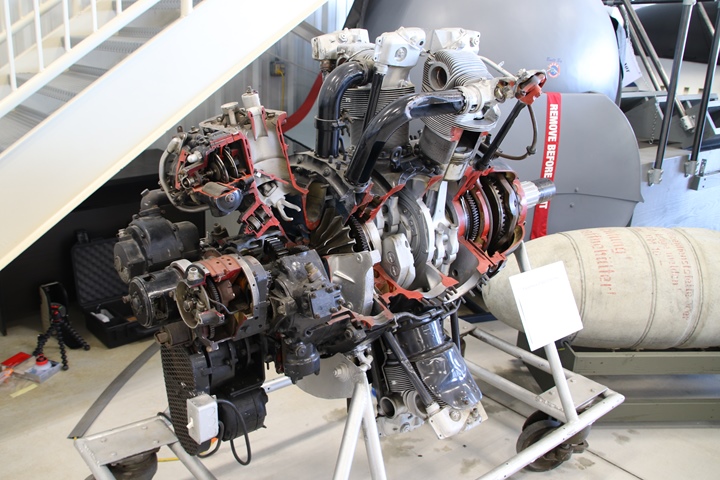
This cut-away of a Pratt & Whitney R-1830 is
on display at the Tri-State Warbird Museum in Batavia, OH. This
could have been manufactured by either Pratt & Whitney or Chevrolet.
Author's photo added 11-19-2020.
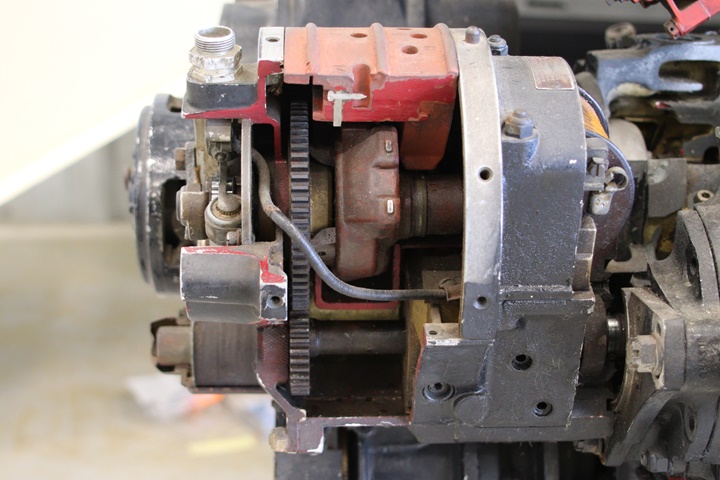
The display has this cut-away of a
Bosch-built magneto, which is the same type Delco-Remy supplied to
Chevrolet under license for this type engine. Author's photo added
11-19-2020.
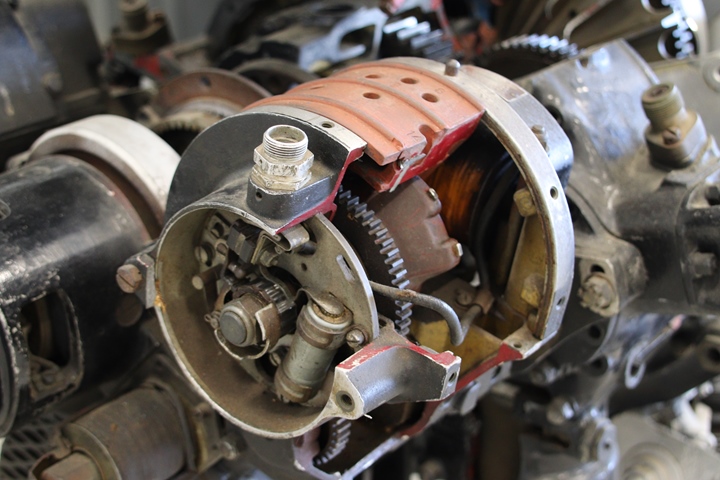
Author's photo added 11-19-2020.
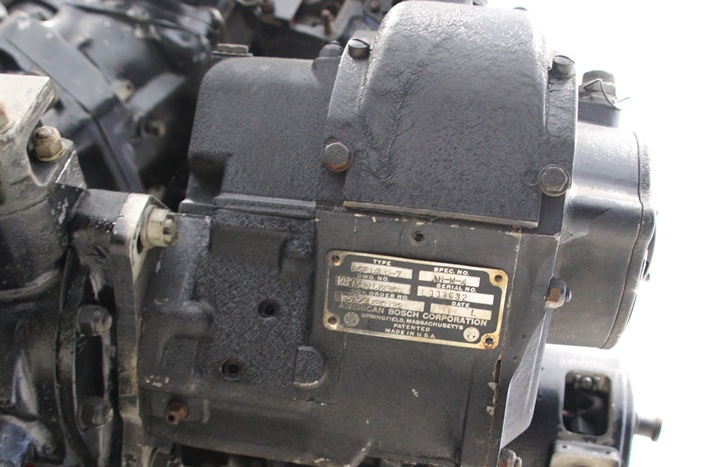
Author's photo added 11-19-2020.
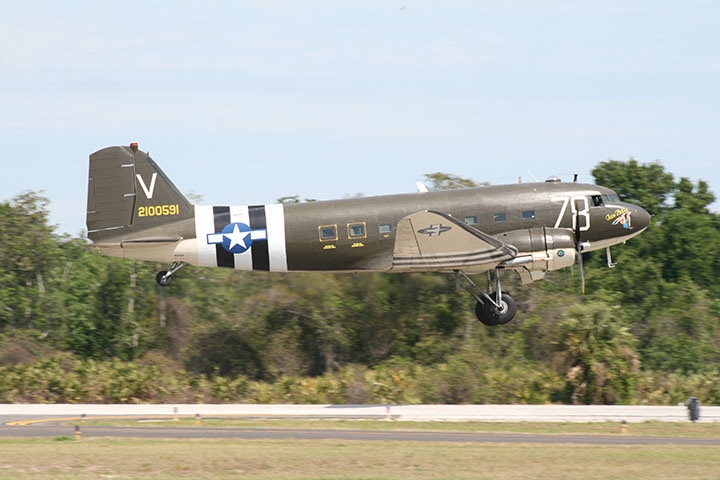
Chevrolet-built R-1830s were used in the
C-47. Author's photo added 5-16-2020.
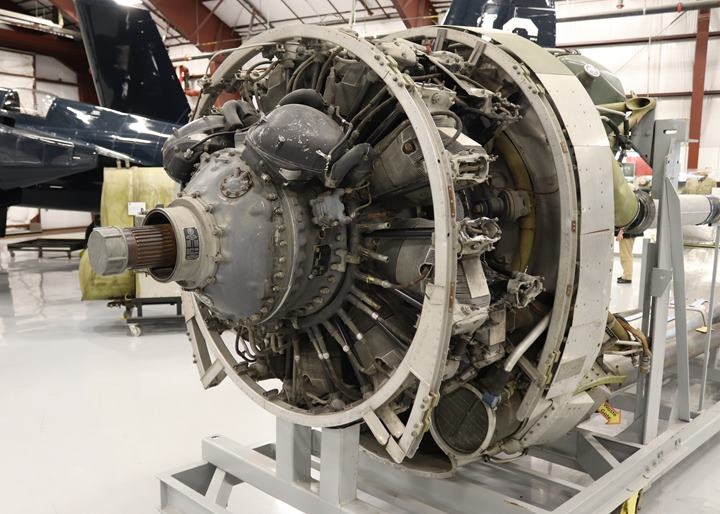
Chevrolet also built the Pratt & Whitney
R-2800 for the war effort. Author's photo added 5-16-2020.
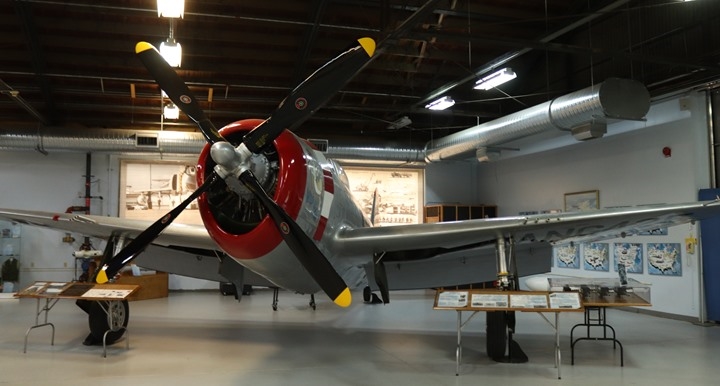
This P-47, located at the Peterson Air and
Space Museum at Peterson AFB in Colorado Springs, CO has a Chevrolet
Tonawanda, NY built R-2800 engine in it. Author's photo added
5-16-2020.
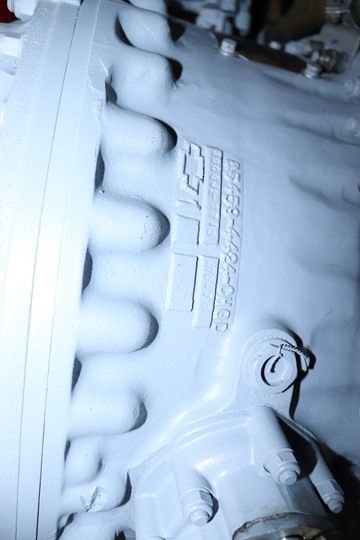
This Chevrolet bowtie is on the engine's
nose housing. Author's photo added 5-16-2020.
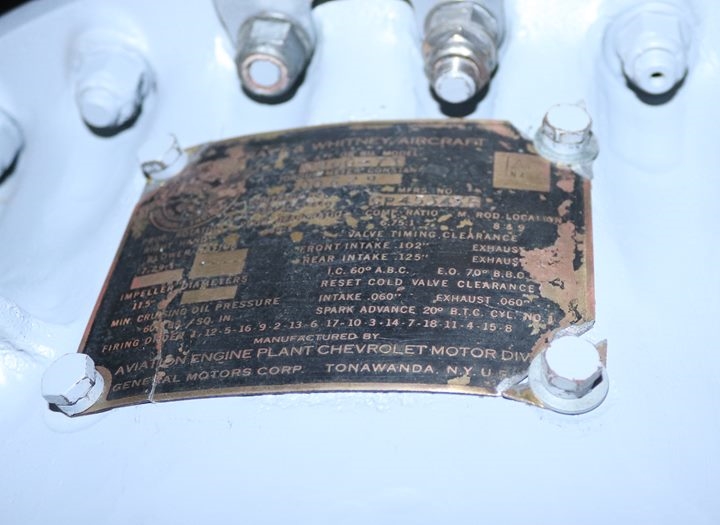
Author's photo added 5-16-2020.
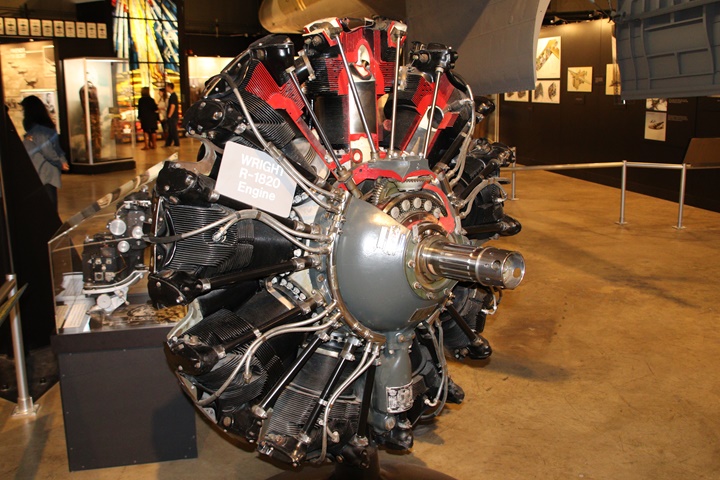
Studebaker built the Wright R-1820 engine
under license. The Studebaker-built R-1820s were only used in the
B-17. Author's photo added 5-16-2020.
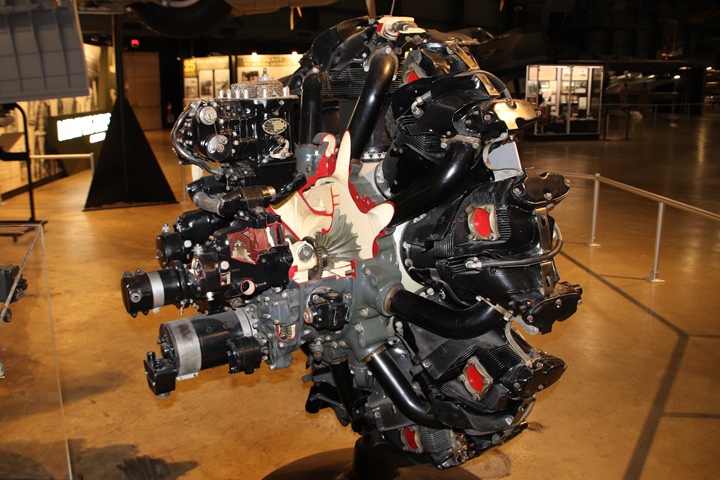
There are two magnetos on each aircraft
engine. Both can be seen at the bottom of the engine.
Author's photo added 5-16-2020.
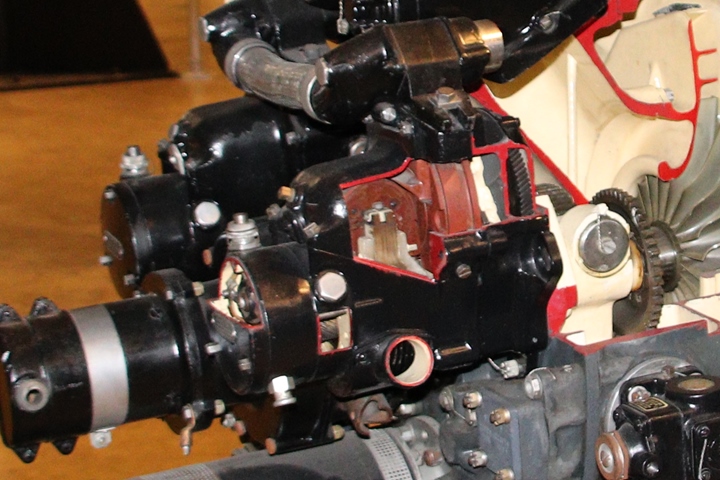
This is a cut-away of a Bosch magneto.
Author's photo added 5-16-2020.
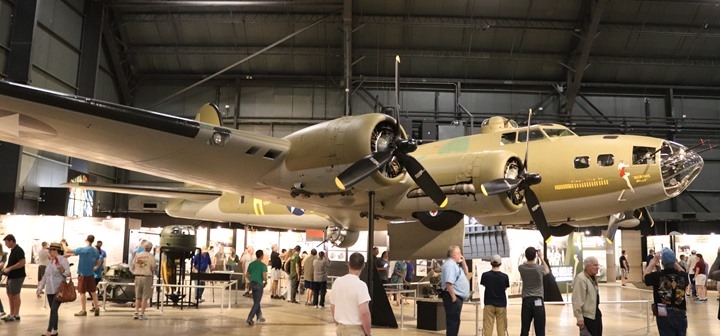
Studebaker engines were used in B-17s, like
the "Memphis Belle" on display at the National Museum of the United
States Air Force. Author's photo added 5-16-2020.
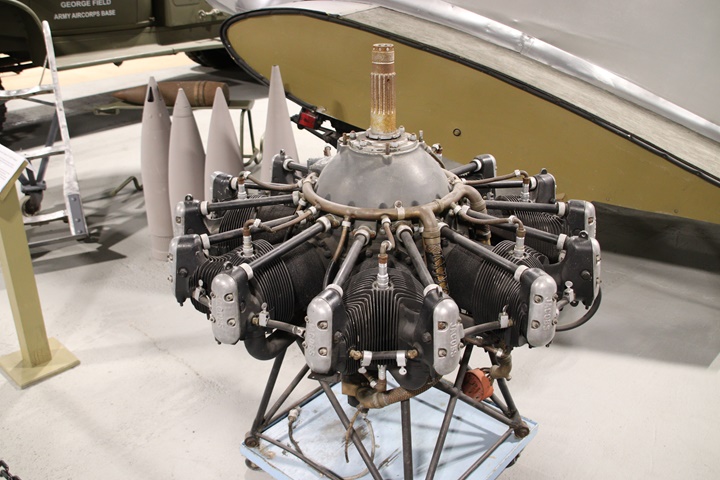
This is a Jacobs R-755 engine.
Author's photo added 5-16-2020.
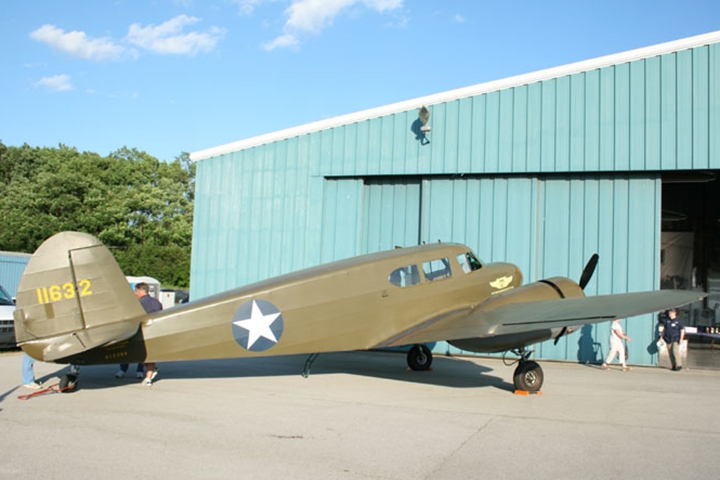
Jacobs engines with Delco-Remy-built
magnetos were used on Cessna T-50 training aircraft. Author's
photo added 5-16-2020.
The Allison V-3420 Twenty-four Cylinder Aircraft
Engine:
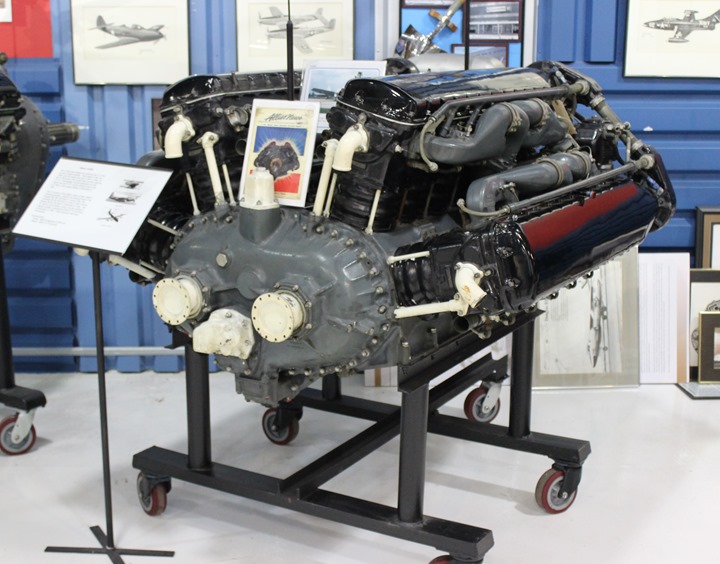
It was announced on June 2, 1944 that Delco-Remy
was supplying the major castings for this aircraft engine, just as it
was doing for the Allison V-1710. This is one of only 150 Allison
V-3420 engines built.
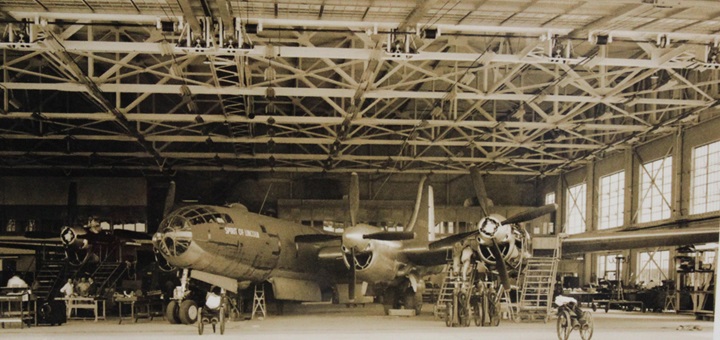
Four of the Allison V-3420 engines with
Delco-Remy castings were installed in a B-29 which was designated the
XB-39. Due to the introduction of the jet engine, the need for a large
piston powered engine vanished at the end of WWII.
The Allison Aircraft
Jet Engine: According to the March 30, 1945 "Delco-Remy Clan," Plant 7 had
been and was providing jet engine castings to Allison. Due to the
secrecy of the project, this was the first time it had been announced to
the employees and public. The April 13, 1945 "Clan" indicated the
Allison-built jet engines were being produced for the Lockheed P-80, the
first operational jet aircraft for the U.S. Army Air Force. The
engine was a GE-designed J-33 centrifugal flow jet engine that Allison
was building under license. Allison built 297 J-33s by the end of
the war.
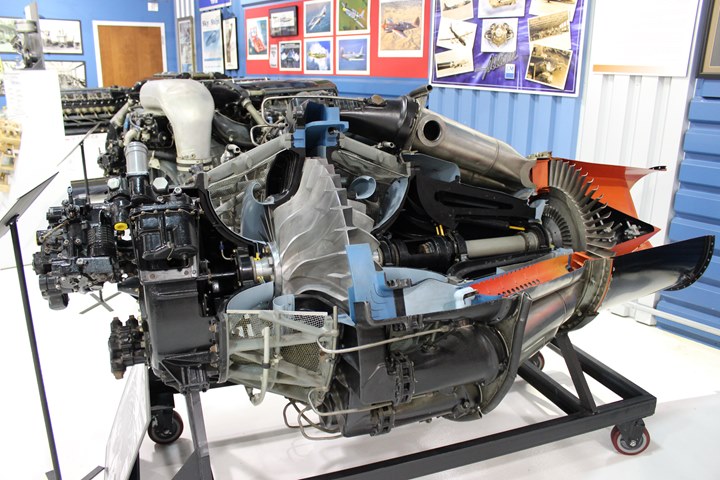
A cutaway of the J-33 which has DR Plant 7
castings in it.
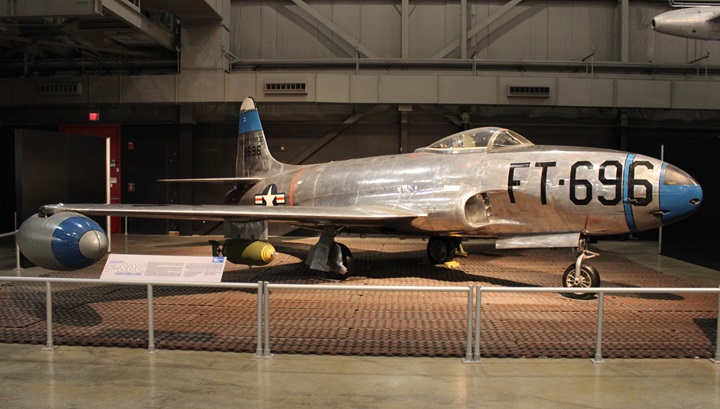
The Lockheed P-80.
|