Delco-Remy in WWII
Delco-Remy WWII Aircraft
Products
Delco-Remy WWII Marine
Equipment
Delco-Remy WWII Tank Products
Delco-Remy WWII Vehicle Products
Delco-Remy and LST-393
Delco-Remy WWII King's Mill
Plant
Delco-Remy WWII Antioch
Foundry
Delco-Remy WWII Stationary Engine Products
Delco-Remy WWII
Electrical Components for the Reo and Federal Truck, 20-Ton, 6x4
Delco-Remy Training Manuals for Aircraft Components
Delco-Remy in World War Two
World War Two Products and
Product Applications
This page updated
4-21-2025.
This is one of four pages
on this site to exhibit the contributions of Delco-Remy Division of GM
in
winning the World War Two. "Delco-Remy at the Normandy Invasion"
details the contribution of the Division during this historic amphibious
invasion. "Our War Job" is the complete reproduction Delco-Remy's
1944 booklet detailing its participation in the war effort up to that
date. "The Army-Navy "E" Award with Three Stars" page is a photo
essay of Delco-Remy's World War Two "E" flag. This page, "World
War Two Products and Product Applications," complements the other three
pages, by providing more detail on the many pieces of equipment which
used Delco-Remy electrical components. Many of these pieces of
equipment were not at the Normandy Invasion. They were
either introduced into the European combat zone after the initial
landings, or obsolete as front line fighting weapons prior to D-Day.
This page has eight more
pages linked at the top that provide more extensive information on
Delco-Remy World War Two products and their applications. There is
too much information to add to one page.
Prior to World War Two,
Delco-Remy not only supplied General Motors cars and trucks with
electrical components, but also supplied other car and truck makers as
well. Even before the United States entered World War Two after
Pearl Harbor, Plant 7 was built in 1940 as an aluminum foundry to
produce castings for the Allison V-1710 aircraft engine. This page shows
many of Delco-Remy (D-R) products used in a plethora of military
applications during World War Two. Product applications fell into four
basic groups: trucks, tracked and wheeled armored vehicles, small
boats and landing craft, and aircraft engines and equipment.
The information on this
and the other eight related pages is not comprehensive but what is known
of applications for Delco-Remy
products during World War Two. There were so many, and after 80
years, it is difficult to find all of the war products D-R built.
This, and the associated application pages, are a good snap-shot of how
Delco-Remy helped win World War Two.
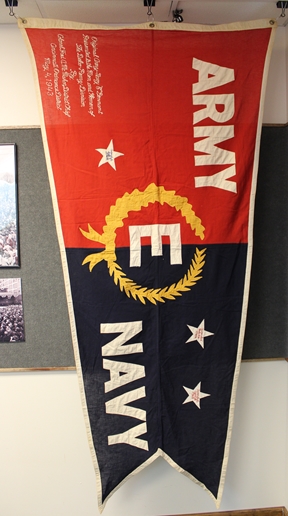
This is the original Anderson Delco-Remy Army Navy "E" Flag that the Division
won during World War Two. This historical treasure was saved for posterity
and was photographed at the Madison County Historical Society's 2016
Delco-Remy display. Authors' photo.
The Army-Navy "E" Award was the most sought after award during World
War Two.
Only 5% of the eligible companies received it. Of those 5%, only 18%
were awarded three stars like D-R Anderson. D-R Anderson
originally won the Army-Navy "E" Award on May 4, 1943. The stars
were added on February 26, 1944, September 9, 1944, and
April 21, 1945.
Delco-Remy
World War Two Products: Table 1 shows that Delco-Remy had a
total of $53,221,000 in major contracts during World War Two. This
total shows the contracts amounts for Anderson, IN, Muncie, IN, and King
Mills, OH. Tables 2 through 5 show the individual contracts for
each of the three locations.
Table 1 - Delco-Remy Division's Major World War Two Contracts
- Total for All Plants
Added 4-21-2025.
The information below
comes from the "Alphabetical Listing of Major War Supply
Contracts, June 1940 through September 1945." This was
published by the Civilian Production Administration, Industrial
Statistics Division.
|
Location |
Contract Amount |
Anderson, IN |
$45,622,000 |
Muncie, IN |
$5,523,000 |
Kings Mills,
OH |
$2,076,000 |
Total |
$53,221,000 |
Table 2 - Delco-Remy Division's Major World War Two Contracts
- Anderson, IN Plants
Added 4-21-2025.
The information below
comes from the "Alphabetical Listing of Major War Supply
Contracts, June 1940 through September 1945." This was
published by the Civilian Production Administration, Industrial
Statistics Division. |
Product - Customer |
Contract Number |
Contract Amount |
Contract Awarded
|
Completion
Date |
Solenoid
Assemblies - USAAF |
535-AC-17676 |
$80,000 |
3-1941 |
11-1941 |
Assemblies
Generator - USAAF |
535-AC-19649 |
$356,000 |
6-1941 |
3-1942 |
Generator
Assemblies - USAAF |
535-AC-20917D |
$1,531,000 |
9-1941 |
5-1943 |
Generator
Assemblies - USAAF |
535-AC-20900D |
$1,115,000 |
9-1941 |
11-1942 |
Starters
Generators - Army Ordnance |
294-ORD-795 |
$267,000 |
10-1941 |
5-1942 |
Generators -
Army Ordnance |
294-ORD-835 |
$173,000 |
3-1942 |
6-1942 |
Cable Systems
90mm AA - Army Ordnance |
294-ORD-956 |
$14,614,000 |
3-1942 |
4-1943 |
Motors
Electrical Servo - USAAF |
535-AC-26141 |
$79,000 |
4-1942 |
12-1942 |
Regulators -
USAAF |
535-AC-26961D |
$339,000 |
6-1942 |
6-1943 |
Air
Compressor Parts - Army Corps of Engineers |
214-ENG-236 |
$50,000 |
7-1942 |
8-1942 |
Generator
Assys - USAAF |
535-AC-27802 |
$1,654,000 |
8-1942 |
6-1944 |
Generators -
USAAF |
535-AC-32312 |
$67,000 |
9-1942 |
5-1943 |
Starter
Motors - Army Ordnance |
294-ORD-1530 |
$608,000 |
10-1942 |
9-1943 |
Generators -
USAAF |
535-AC-33621 |
$50,000 |
11-1942 |
4-1943 |
Generator
Assys - USAAF |
535-AC-33161 |
$12,239,000 |
11-1942 |
12-1943 |
Generator
Assemblies - USAAF |
535-AC-33968 |
$3,335,000 |
2-1943 |
12-1943 |
Generator
Parts - USAAF |
535-AC-37743 |
$80,000 |
2-1943 |
8-1943 |
Generators -USAAF |
2229-AC-43 |
$78,000 |
2-1943 |
11-1943 |
Electrical
Equipment - USAAF |
535-AC-35765 |
$157,000 |
2-1943 |
12-1943 |
Batteries -
Navy |
S-10212 |
$94,000 |
2-1943 |
11-1943 |
Communication
Equipment - Army Signal Corps |
3435-SC-330 |
$50,000 |
6-1943 |
4-1944 |
Voltage
Regulators - USAAF |
33038-AC-290 |
$825,000 |
8-1943 |
7-1944 |
Generator
Assys - USAAF |
20017-AC-57 |
$1,564,000 |
9-1943 |
6-1944 |
Elec
Generator Assys - USAAF |
30053-AC-347 |
$486,000 |
12-1943 |
10-1944 |
Batteries -
Army Ordnance |
33008-ORD-693 |
$205,000 |
1-1944 |
12-1944 |
Ordnance
Equipment - Army Ordnance |
33008-ORD-590 |
$74,000 |
2-1944 |
10-1944 |
Storage
Batteries - USAAF |
33038-AC-2021 |
$69,000 |
2-1944 |
10-1944 |
Regulators - USAAF |
33038-AC-1784 |
$429,000 |
2-1944 |
5-1945 |
Industrial
Truck Parts - Army Quartermaster Corps |
12036-QM-3896 |
$56,000 |
3-1944 |
2-1945 |
Ordnance
Equipment - Army Ordnance |
33008-ORD-624 |
$123,000 |
3-1944 |
1-1945 |
Electric Gen
Assys - USAAF |
33038-AC-1789 |
$1,156,000 |
3-1944 |
4-1945 |
Ordnance
Equipment - Army Ordnance |
33008-ORD-958 |
$231,000 |
5-1944 |
5-1945 |
Motor Vehicle
Parts - U.S. Treasury Deparment |
TPS-55774L |
$154,000 |
6-1944 |
10-1944 |
Generator Assys - USAAF |
33038-AC-2908 |
$728,000 |
6-1944 |
10-1945 |
Storage
Batteries - Army Ordnance |
33008-ORD-1298 |
$258,000 |
8-1944 |
5-1945 |
Electrical
Equipment - Army Ordnance |
33008-ORD-1520 |
$70,000 |
9-1944 |
7-1945 |
Electrical
Equip - Army Ordnance |
33008-ORD-1519 |
$268,000 |
9-1944 |
9-1945 |
Motor
Generator Parts - Army Ordnance |
33008-ORD-1781 |
$285,000 |
12-1944 |
7-1945 |
Batteries -
Army Ordnance |
33008-ORD-1690 |
$1,608,000 |
12-1944 |
7-1945 |
Generator
Parts - Army Corps of Engineers |
33017-ENG-660 |
$64,000 |
12-1944 |
6-1945 |
Diesel
Starting Motors - Navy |
OBS-20235 |
$101,000 |
1-1945 |
7-1945 |
Motor Vehicle
Parts - Navy |
OM-47260 |
$60,000 |
1-1945 |
7-1945 |
Electric
Generators Motors - Army Corps of Engineers |
33017-ENG-1966 |
$65,000 |
3-1945 |
10-1945 |
Electric Gen
Assys - USAAF |
33038-AC-8976 |
$226,000 |
5-1945 |
12-1945 |
Generator
Assys - USAAF |
33038-AC-8503 |
$607,000 |
5-1945 |
12-1945 |
Voltage
Regulators - USAAF |
33038-AC-9778 |
$617,000 |
5-1945 |
3-1946 |
Voltage
Regulators - USAAF |
33038-AC-8391 |
$363,000 |
5-1945 |
8-1945 |
Electrical
Equip - Army Quartermaster Corps |
12036-QM-18689 |
$148,000 |
6-1945 |
6-1946 |
Total |
|
$47,856,000 |
|
|
Minus
Batteries built in Muncie Awarded to Anderson. From
Table 3. |
|
$2,234,000 |
|
|
Corrected
Anderson-built Total |
|
$45,622,000 |
|
|
Of special interest in Table
2 is contract Army Ordnance contract number 294-ORD-956 for $14,614,000
for 90mm anti-aircraft gun cables. The $14,614,000 is 32% of the
total contracts awarded to the Anderson plants. What is of special
interest is that cables were not a Delco-Remy core product like the
generators, regulators, and starters that were contracted to the
Anderson plants. As the information from "Our War Job" below
shows, Plant 8 was in the process of tooling up for this project when it
was cancelled. Because this was not a core product, Delco-Remy had
to have sub-contractors provide the components for final assembly in
Plant 8. No doubt this was part of the reason why the project was
cancelled, as this was a timely process.
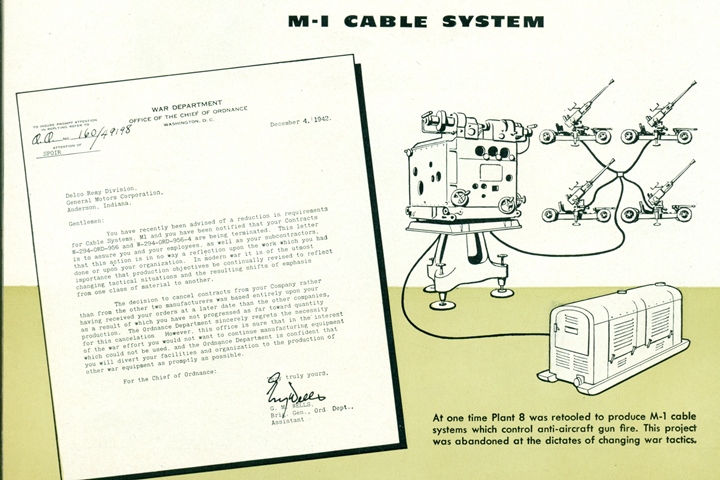
Image added 4-21-2025.
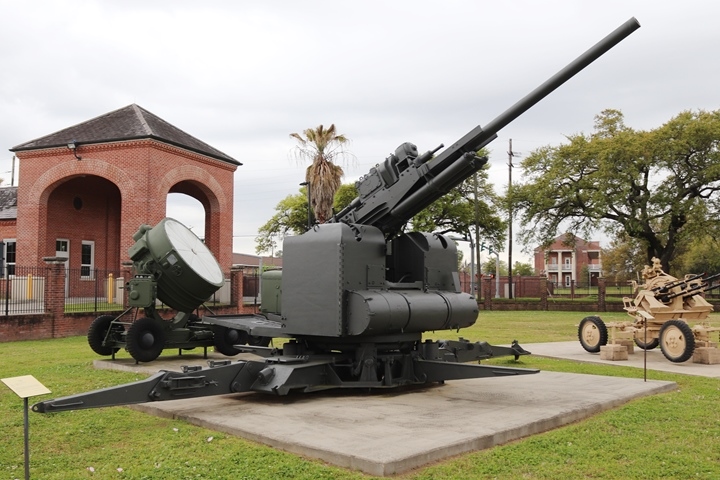
The Delco-Remy document shows 40mm
anti-aircraft guns using the cable. The contract was for M-1
cables to be used with 90mm anti-aircraft guns like the one shown here.
Author's photo added 4-21-2025.
Table 3 - Delco-Remy Major World
War Two Battery Contracts awarded to the Anderson, IN Plants but
actually built in the Muncie, IN Battery Plant
Added 4-21-2025.
The information below
comes from the "Alphabetical Listing of Major War Supply
Contracts, June 1940 through September 1945." This was
published by the Civilian Production Administration, Industrial
Statistics Division. |
Product - Customer |
Contract Number |
Contract Amount |
Contract Awarded
|
Completion
Date |
Batteries -
Navy |
S-10212 |
$94,000 |
2-1943 |
11-1943 |
Batteries -
Army Ordnance |
33008-ORD-693 |
$205,000 |
1-1944 |
12-1944 |
Storage
Batteries - USAAF |
33038-AC-2021 |
$69,000 |
2-1944 |
10-1944 |
Storage
Batteries - Army Ordnance |
33008-ORD-1298 |
$258,000 |
8-1944 |
5-1945 |
Batteries -
Army Ordnance |
33008-ORD-1690 |
$1,608,000 |
12-1944 |
7-1945 |
Total |
|
$2,234,000 |
|
|
Table 4 - Delco-Remy Division's Major World War Two Contracts
- Muncie, IN Battery Plant
Added 4-21-2025.
The information below
comes from the "Alphabetical Listing of Major War Supply
Contracts, June 1940 through September 1945." This was
published by the Civilian Production Administration, Industrial
Statistics Division. |
Product - Customer |
Contract Number |
Contract Amount |
Contract Awarded
|
Completion
Date |
Batteries Storage - Naval Aeronautics |
XSA-13364L |
$249,000 |
10-1942 |
2-1944 |
Batteries - U.S. Treasury Department |
TPS-22801L |
$101,000 |
12-1942 |
7-1943 |
Batteries - Army Ordnance |
294-ORD-2212 |
$163,000 |
3-1943 |
3-1944 |
Batteries - Navy |
288-S-17403 |
$122,000 |
10-1943 |
6-1944 |
Batteries - Navy |
288-S-18261 |
$171,000 |
11-1943 |
11-1944 |
Battery Vent Caps - Navy |
288-S-20416 |
$74,000 |
2-1944 |
8-1944 |
|
33008-ORD-760 |
$323,000 |
3-1944 |
4-1945 |
Batteries - U.S. Treasury Department |
TPS-52225L |
$92,000 |
3-1944 |
6-1944 |
Storage Battery Caps - Naval Aeronautics |
288-XSA-21862 |
$185,000 |
4-1944 |
9-1944 |
Storage Batteries - Naval Aeronautics |
288-XSA-22102 |
$290,000 |
4-1944 |
5-1945 |
Storage
Batteries - Naval Aeronautics |
288-XSA-22479 |
$182,000 |
4-1944 |
12-1945 |
Storage
Batteries - Army Ordnance |
33008-ORD-714 |
$60,000 |
5-1944 |
9-1944 |
Storage
Batteries - Army Ordnance |
33008-ORD-1269 |
$143,000 |
8-1944 |
5-1945 |
Dry Cell Batteries - Army Ordnance |
33008-ORD-1850 |
$250,000 |
11-1944 |
6-1945 |
Storage Batteries - Naval Aeronautics |
XSA-95379 |
$352,000 |
3-1945 |
4-1946 |
Storage Batteries - Naval Aeronautics |
XSA-95423 |
$154,000 |
4-1945 |
6-1945 |
Battery Vents - Naval Aeronautics |
288-XSA-33087 |
$108,000 |
6-1945 |
1-1946 |
Total |
|
$3,019,000 |
|
|
Plus
Batteries built in Muncie Awarded to Anderson. From
Table 3. |
|
$2,234,000 |
|
|
Corrected
Muncie-built Total |
|
$5,523,000 |
|
|
Table 5 - Delco-Remy Division's Major World War Two Contracts
- Kings Mill, OH Landing Craft Starter Motor Plant
Added 4-21-2025.
The information below
comes from the "Alphabetical Listing of Major War Supply
Contracts, June 1940 through September 1945." This was
published by the Civilian Production Administration, Industrial
Statistics Division. |
Product - Customer |
Contract Number |
Contract Amount |
Contract Awarded
|
Completion
Date |
Diesel Engine
Motors - Navy Ships Bureau |
OBS-14704 |
$2,076,000 |
5-1944 |
6-1945 |
Total |
|
$2,076,000 |
|
|
During World War Two, companies were not
allowed to publicly publish production numbers, as they were
considered to be a military secret. In 1945 these regulations
eased up. In the February 9,1945 edition of the "Delco-Remy Clan,"
Delco-Remy was allowed to release production numbers of World War Two products to
date. The numbers are shown by general product groups and not by
individual product; but they do give an insight into the amount of war material D-R
produced up until early 1945.
The plants included in the production of the following parts were
Anderson, IN; Bedford, IN; Kings Mill, OH; Muncie, IN; and Yellow
Springs, OH. No specifics are given below for the number of
batteries produced by Muncie.
1,500,000+ electrical sets consisting of generators, cranking motors,
regulators, switches, distributors and coils for military trucks,
tractors and DUKWs.
485,000+ heavy duty of generators, cranking motors, regulators, coils
and switches for Army tanks and tank destroyers and for Navy landing
craft and PT boats.
105,000+ aircraft generators and regulators.
295,000+ aircraft magnetos. Two magnetos were used per aircraft
engine. During World War Two, 812,615 aircraft engines were produced.
DR supplied over 147,500 or 18% of them with magnetos.(62,000+ aircraft engine controls.
40,000+ Sperry automatic pilot servo controls.
60,000+ complete sets of aluminum castings for the Allison V-1710 and
V-3420 aircraft engines. Allison produced (69,305) V-1710 and
V-3420 engines during World War Two.
-
Further research indicates that Delco-Remy
also supplied: 2,196 marine pitch propeller controls for 1,098 Landing Craft,
Infantry, (Large) and 544 units for 243 110-foot subchasers.
-
There was an unknown amount of supercharger blowers
produced for Detroit Diesel Division of
General Motors 6-71 engines that were used on Sherman tanks, Wolverine
tank destroyers, and most small landing craft used in World War Two.
In July 1943 Delco-Remy had a run rate of 6,500 blowers per month.
Delco-Remy World War Two Products by Plant
|
Plant |
Product |
World War Two Document |
Comments |
1 |
Marine propeller pitch control switch, aircraft
magneto coils, bomber trim tab controls |
Propeller Shifter Switch |
|
2 |
Aircraft magneto molded parts and breaker
assemblies |
|
|
3 |
Marine propeller pitch control motor |
|
|
4 |
Servo bodies for aircraft auto-pilots |
|
|
5 |
Various castings |
|
|
6 |
Contact point regulators, Carbon pile aircraft
regulators, automatic engine control |
Carbon Pile Regulators |
|
7 |
Aluminum foundry for aircraft castings |
|
Allison V-1710 aircraft engine |
8 |
Aircraft generators |
|
|
9 |
Steel tubing, aircraft storage batteries,
supercharger blowers |
|
Steel tubing for fuel, oil, air, brake,
refrigerator, and electrical conduit |
10 |
Bosch aircraft magnetos, aircraft machined parts |
|
|
Yellow Springs, OH (Antioch) |
Aluminum foundry for aircraft castings,
experimental casting work |
|
|
Bedford, IN |
Aluminum foundry for aircraft castings |
|
|
Midwest |
Packaging and shipping |
|
|
Kings Mill, OH |
Marine starter motors for landing craft |
|
|
PT-305:
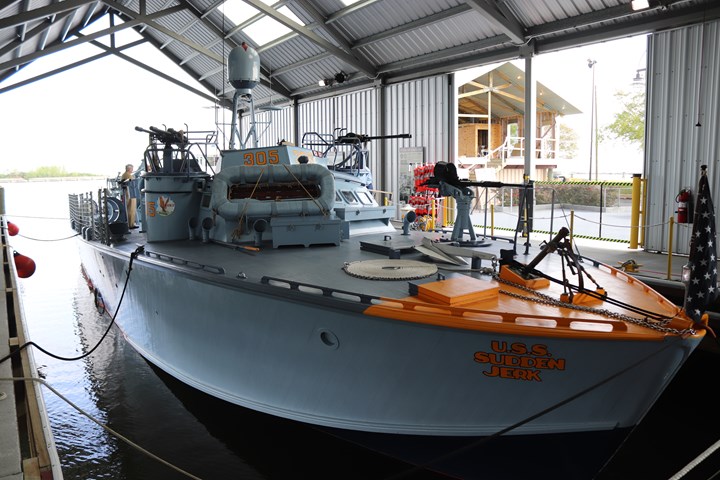
PT-305 is the only operating Higgins-built
PT boat that is a World War Two combat veteran. The three 1,500 hp Packard
marine engines have D-R cranking motors and DC generators.
Author's photo added 3-29-2018.
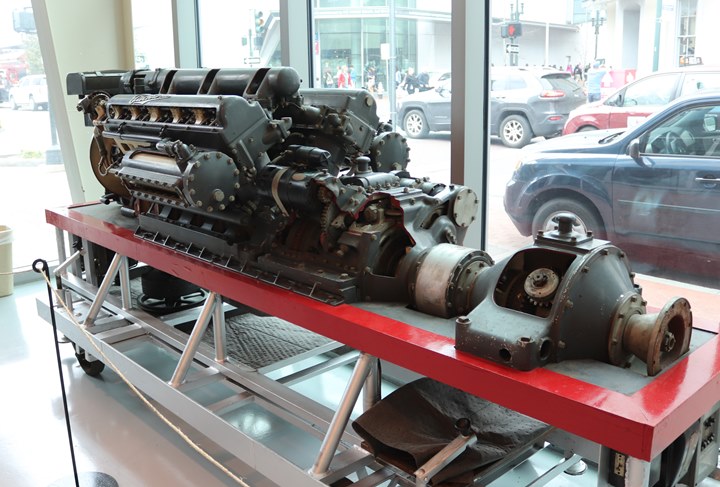
The National World War Two Museum in
downtown New Orleans, LA has this cut-a-way of a Packard marine engine
on display which was used to power the World War Two PT boats. A Delco-Remy
starter is prominently displayed on the engine.
Author's photo added 3-29-2018.
LST-393:
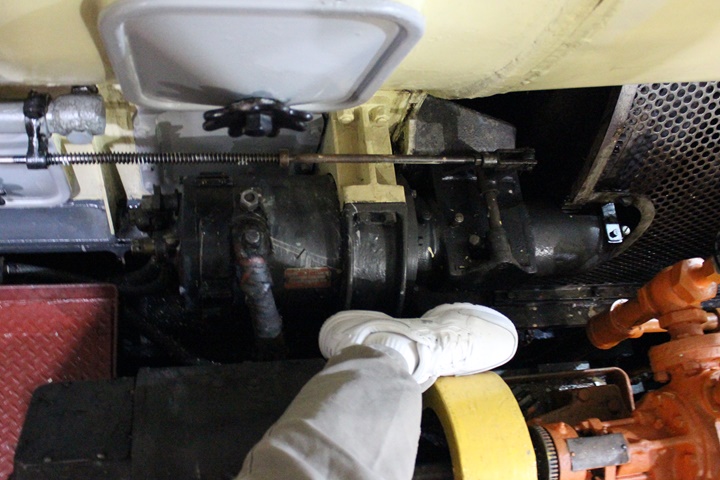
Now this is a Delco-Remy cranking motor!!!
Note the size of the motor compared to the author's size 9-1/2 shoe.
It took this size of a cranking motor to start the Electro-Motive 900 hp
diesel engine on US Navy LST landing ships. This and a second D-R
starter can be seen on LST 393 in Muskegon, MI. Author's photo.
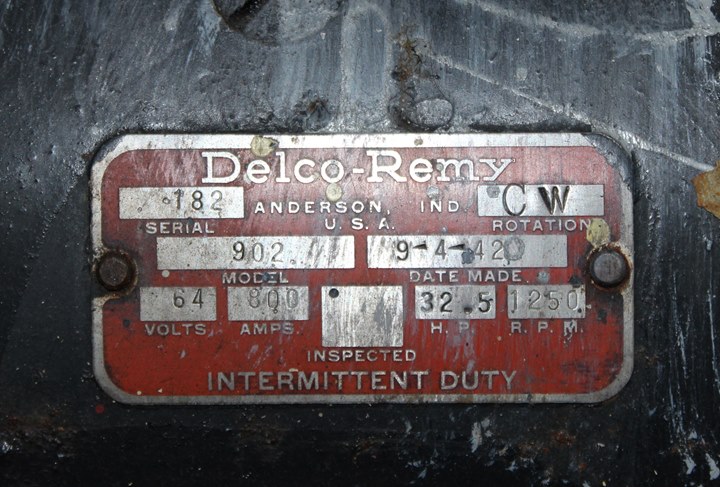
The Delco-Remy ID Tag shows that this was
Serial Number 182 and built on 9-4-1942. This 64 volt starter
pulled 800 amps to produce 32.5 hp. This is the largest D-R
cranking motor the author has ever seen. For more photos and
information see my
D-R World War Two LST 393 page. Author's photo.
The B-29 Project: Delco-Remy was
one of seventeen GM Divisions that built components for the B-29.
It was the most expensive project of World War Two, being even more expensive
than the Manhattan Project.
No mention of the B-29 is made in the 1944
Delco-Remy booklet "Our War Job". There are two reasons for this.
First, production on the B-29 did not start until mid-1944, and
contracts and tooling were still being made when the booklet was
published. Second, the B-29 project was considered "Top Secret."
Delco-Remy would have only been able to state it was working on the
project, but not what the project was. As diverse as Delco-Remy
produced
aircraft-related products were during World War Two, the Division
could have supplied any number of components for the B-29.
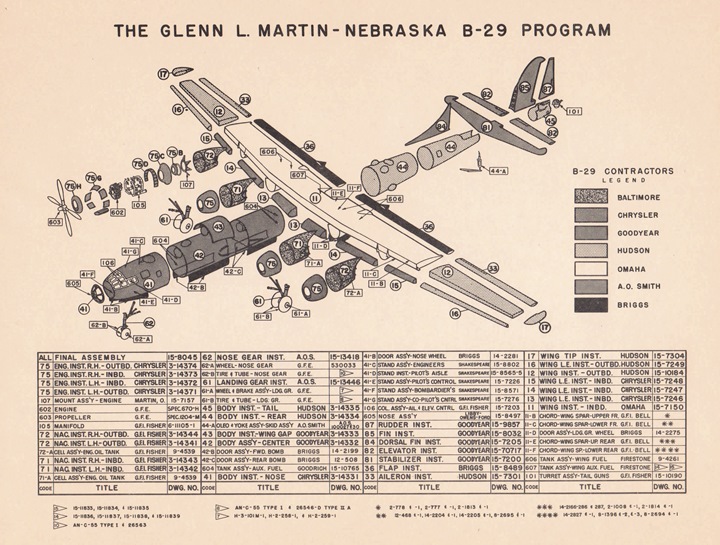
This Glenn Martin Company document shows the major airframe suppliers
for its plant in Omaha, NE. This was one of four plants that
produced the B-29 during World War Two. The Omaha plant relied on
the American auto industry for many of the components for the B-29s it
built.
Starting at the front of
the fuselage and working towards the rear of the aircraft, the glass
nose section was built by Libby-Owens-Ford, an automotive glass company.
The fuselage nose section was built by Chrysler's Plymouth Division in
Detroit. Goodyear in Akron, OH built the two bomb bay fuselage
sections. Briggs, an independent auto body manufacturer in
Detroit, provided the bomb bay doors. The three rear fuselage
sections behind the wings were also built in the city of Detroit by the
Hudson Motor Car Company, which combined with Nash in 1954 to become
American Motors. The entire tail section and the elevators with
control surfaces were made by Goodyear, and the tail gunner's position
was manufactured by the Fisher Body Division of GM at Cleveland, OH.
Martin Omaha provided the
center section of the wing. Chrysler provided the inboard leading
edges. Hudson built the outer wing sections, outer leading edges,
ailerons, and wing tips. Briggs provided the flaps. All four
engine nacelles and engine oil tanks came from the Fisher Body Division
of GM along with the exhaust manifolds. Omaha built the engine
mounts; Dodge supplied the engines and Chrysler the engine cowlings.
Firestone provided the
main and auxiliary wing fuel tanks. BF Goodrich provided the fuselage
auxiliary fuel tank.
While this is a Boeing-designed aircraft, there are no major fuselage, wing
nor rear tail
section components provided by that company for the Martin Omaha-built
B-29s. With the exception of
the Martin wing center section, the rest of the wing was supplied by the
American automobile industry.
Inside the B-29 airframe
and wing structural components listed above, there were tens of
thousands of parts and components. The engine nacelles produced by
the Fisher Body Division of GM had over 3,000 parts in them. Each
nose fuselage section built by Chrysler had 5,000 parts in it.
Many of the parts for many of the major components would have been
supplied by AC Sparkplug, Allison, Brown-Lipe-Chapin, Buick, Chevrolet,
Delco Appliance, Delco Products, Delco Radio, Delco-Remy, Fisher Body,
Frigidaire, Harrison Radiator, Hyatt Bearings, Moraine Products, New
Departure, Packard Electric, and Rochester Products Divisions of GM as
identified in the 1944 GM Annual Report.
Of significance is that
the Martin Plant in Omaha, NE produced the Silverplate B-29 Nuclear
Bombers.
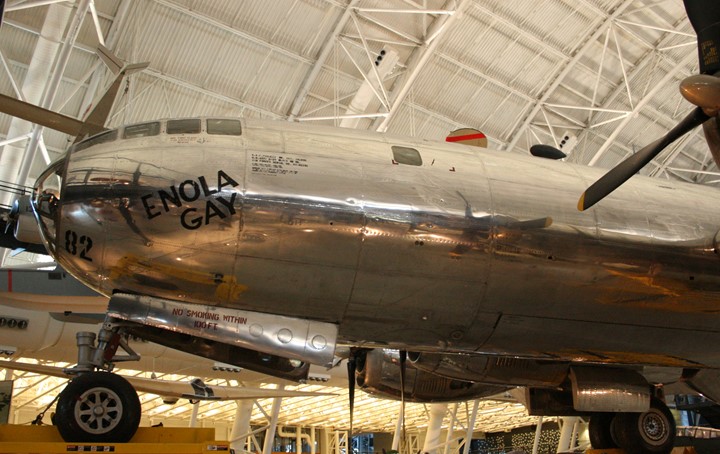
No doubt some Delco-Remy part or component
went on a ride to Hiroshima, Japan in the Enola Gay on August 6, 1945.
Author's photo.
Delco-Remy
World War Two Products as listed in "Our War Job:" Electrical Components for
Military Trucks - Generators and generator regulators, starting motors,
ignition distributors and coils, switches, and batteries; Electrical
Components for Military Tanks and Armored Vehicles - Generators and
generator regulators, starting motors, ignition distributors and coils,
apparatus boxes, and batteries; Electrical Components for Military
Aircraft - Generators and generator regulators, magnetos, and batteries;
Automatic Aircraft Engine Controls; Solenoids for Sperry Autopilots;
Automatic Trim Tab Controls; Electrical Components for Military Marine
applications - Generators and generator regulators, starting motors,
ignition distributors and coils; Marine propeller pitch controls
for landing craft and submarine chasers; Marine diesel equipment -
pistons, blowers, pre-heaters and pre-heater fuel pumps, governors;
Tubing - for electrical, fuel, brake, air conditioning, oil and air
lines; Allison V-1710 engine castings - Various; Aircraft engine
machined parts - Various; (1,000,000) 20mm shell bodies; Various
solenoids for starting motors, aircraft bomb release racks, guns and
overdrive controls.
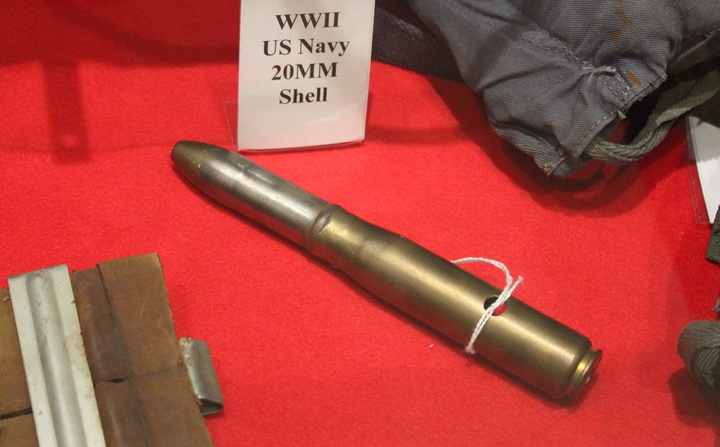
Delco-Remy manufactured one million 20mm
shell projectiles. The U.S. Navy was the primary user of the 20mm
cannon during World War Two. Author's photo added 5-8-2020.
Delco-Remy
World War Two Products at the Madison County Historical Society:
The Madison County Historical Society in Anderson, IN has an excellent
collection of Delco-Remy-built World War Two era components. Below
are photos from the 2016 Delco-Remy exhibit at the historical society.
Some of the parts are experimental, and others production items.
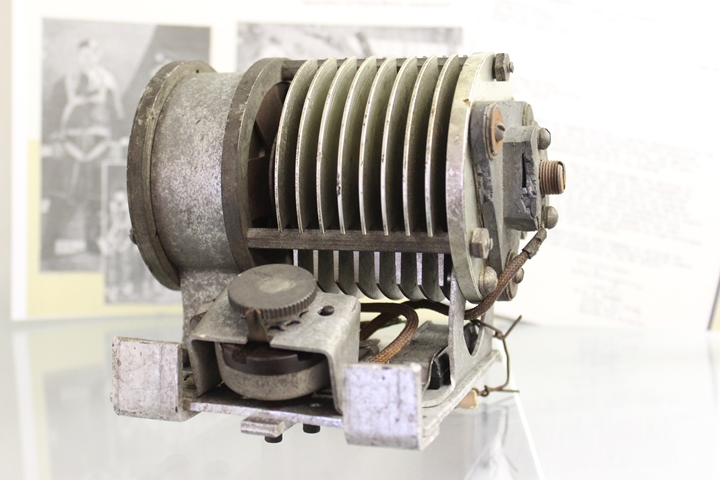
This is a carbon pile aircraft regulator.
It was developed by Delco-Remy. At the request of the U.S. Army
Air Force, Delco-Remy then licensed to other manufacturers to assure an
adequate supply. Author's photo added 5-8-2020.
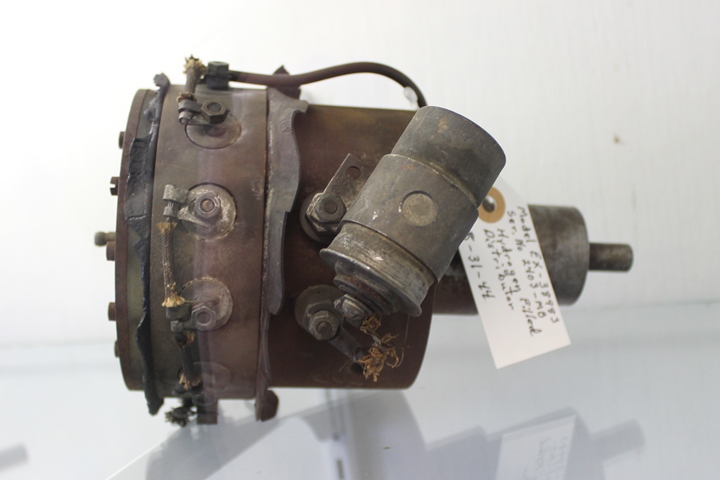
This is an experimental hydrogen filled
distributor model number EX-38983. Author's photo added 5-8-2020.
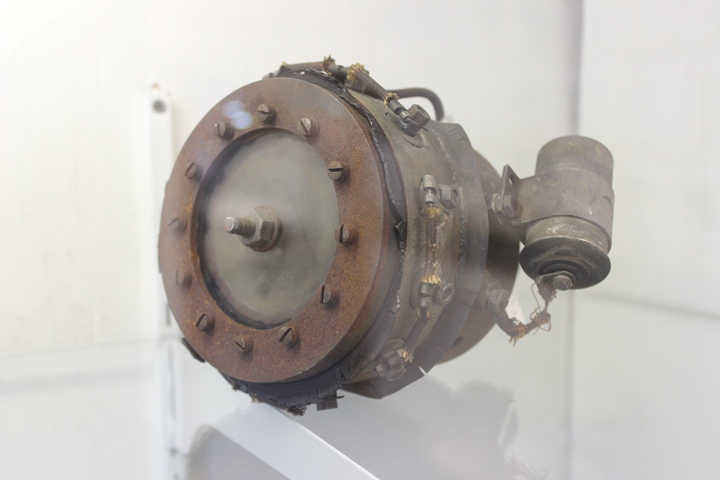
Model number EX-38983 as seen from the
bottom. Author's photo added 5-8-2020.
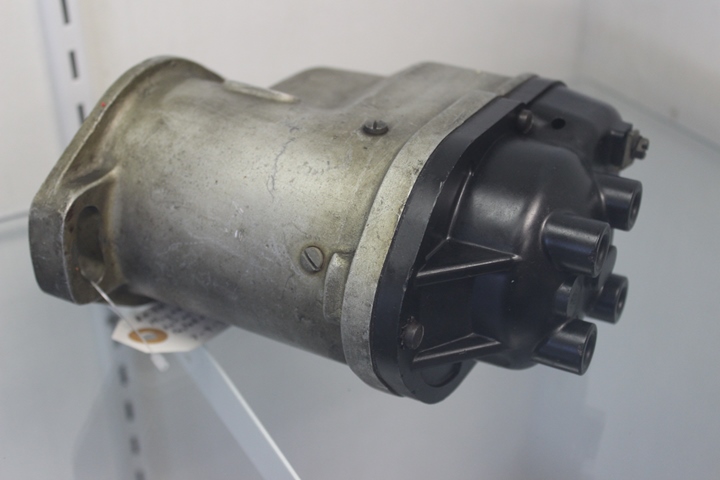
Experimental four-cylinder magneto with
partial model number EX-3674x. It is of 1941 vintage.
Author's photo added 5-8-2020.
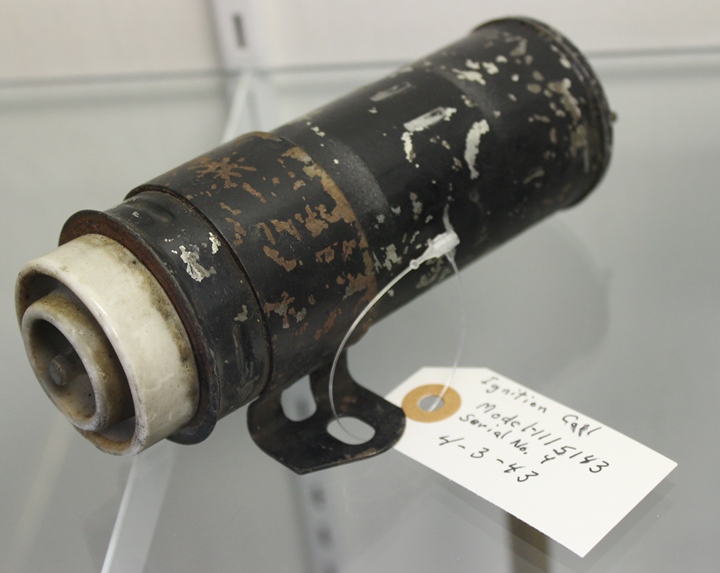
Ignition coil 1115143 is also part of the
collection. Author's photo added 5-8-2020.
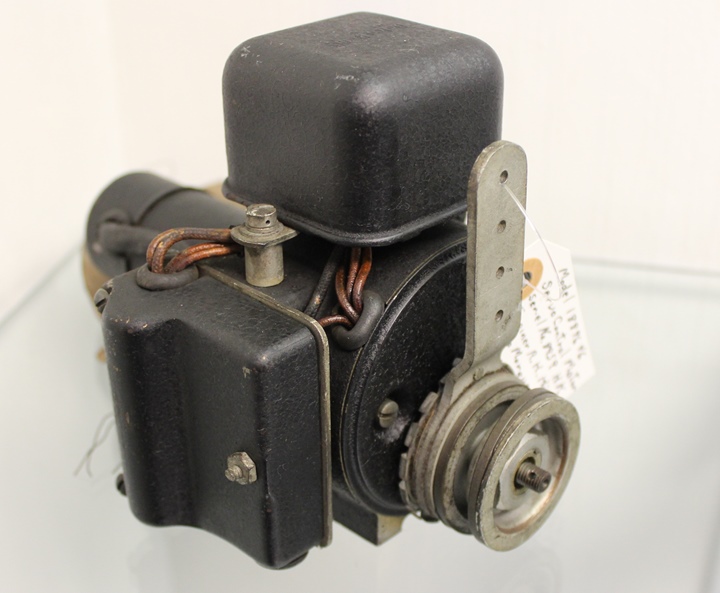
The servo control motor on display at the
Historical Society is model number 1889646 with serial number 8959hk. This
was part of the Sperry auto-pilot that Delco-Remy produced for such aircraft
as the B-24 Liberator bomber. Author's photo added 5-8-2020.
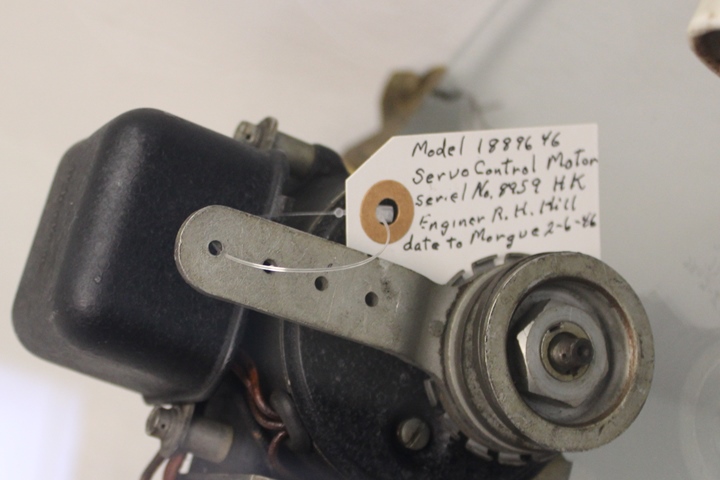
Author's photo added 5-8-2020.
World War Two Experimental Alternator:
This Delco-Remy engineering sample was found on the 1943 Chevrolet
Airborne Extra-Light 1/4-Ton Jeep Program. More photos and
information can be found on the
Delco-Remy Military
Truck page.
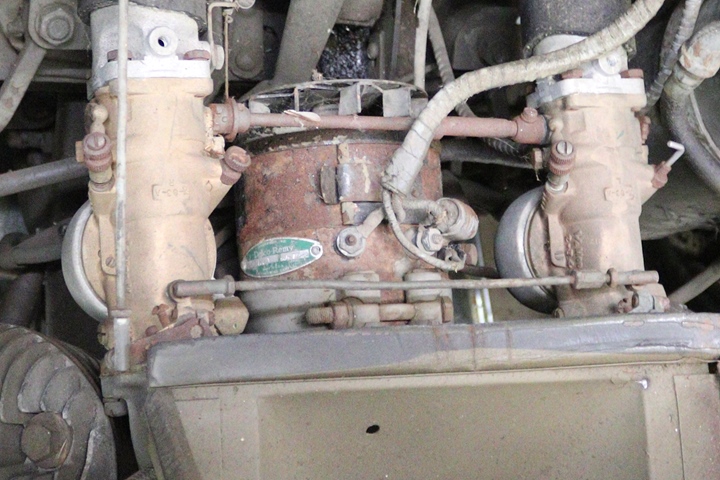
This has all of the appearances of a
Delco-Remy alternator. Author's photo added 5-8-2020.
Delco-Remy Clan Photos:
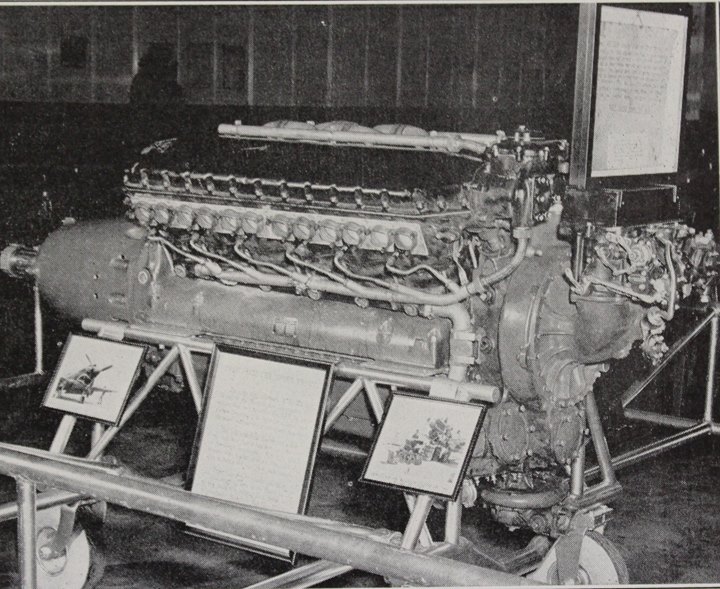
This Allison V-1710 was on display at
Delco-Remy in
February 1942. It came back from Libya with five bullet holes in
the nose housing. The Royal Air Force P-40 Tomahawk was able to
land safely.
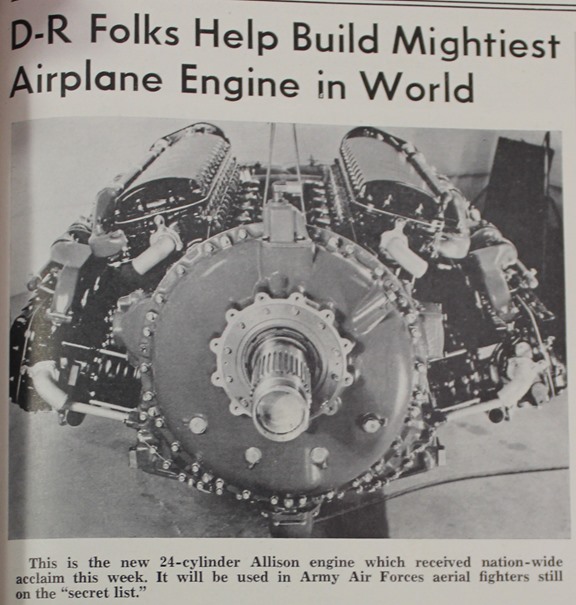
This is the Allison V-3420 engine as shown
in the 'Delco-Remy Clan' dated June 2, 1944. Only 160 were made,
of which four
were used to replace the R-3350 engines on a test B-29. The coming
of jet propulsion doomed this engine. Delco-Remy Plant 7 provided
many of the Aluminum castings for the limited run of the engine.
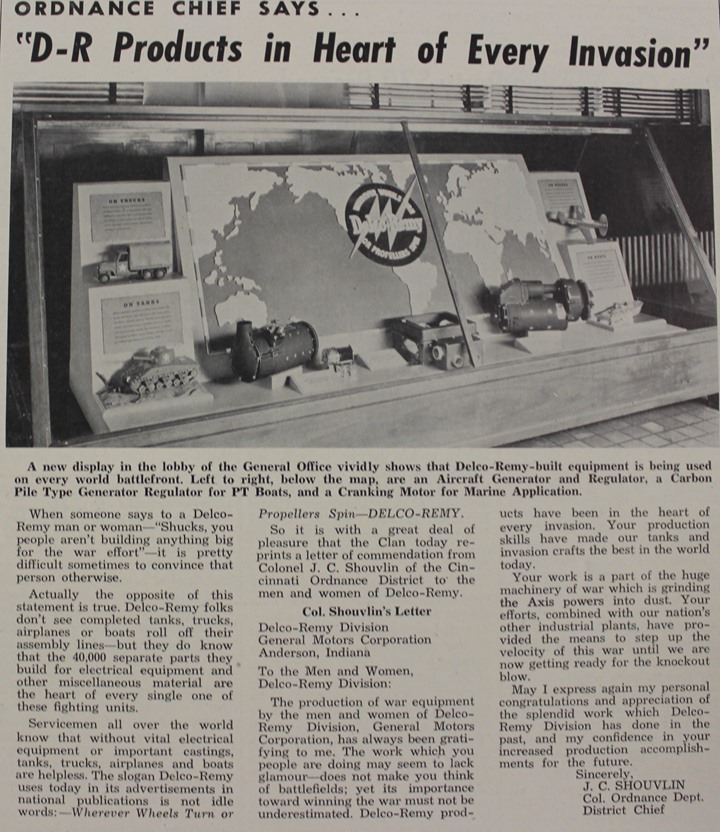
From the March 9, 1945 'Delco-Remy Clan.'
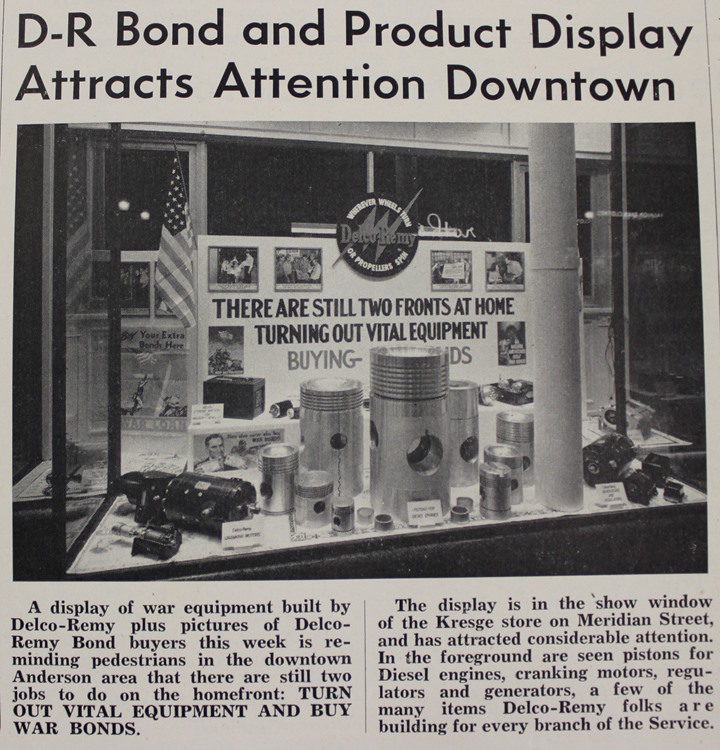
From the June 1, 1945 'Delco-Remy Clan.'
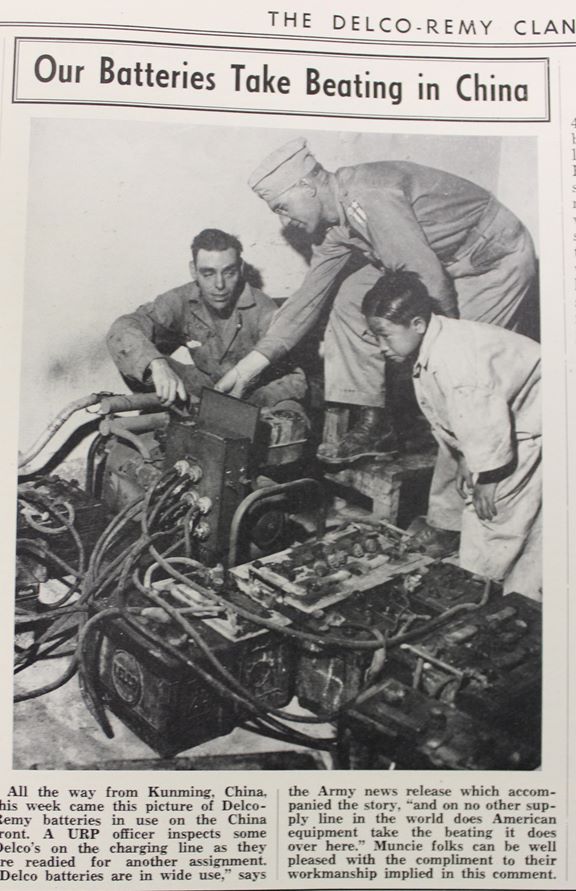
Bedford,
IN: It was announced in the August 14, 1944, issue of the
'Delco-Remy Clan'
that Delco-Remy had purchased the Salem and Walters Mills and the
property of the Indiana Lime Stone Company in Bedford, IN. The new
plant became the Bedford Foundry Plant of the Delco-Remy Division.
The complex consisted of two mill buildings totally 140,000 square feet
and an office building. It, along with plant 7 in Anderson,
produced aluminum castings for the Allison aircraft engine.
According to the March 9,
1945 edition of the 'Delco-Remy Clan,' Bedford had received new contracts
for increasing production on the Rolls-Royce aircraft engine. This
implies that Bedford had already been producing casting for the Packard-built Rolls-Royce V-1650 Merlin engine. This is the only reference
I have ever seen that Delco-Remy was supplying castings to any other
aircraft engine manufacturer besides Allison. The Packard-built
Merlin engine was the most important and best engine used in an Army Air
Force fighter during World War Two. It made the P-51 Mustang into
the best Army World War Two fighter aircraft.
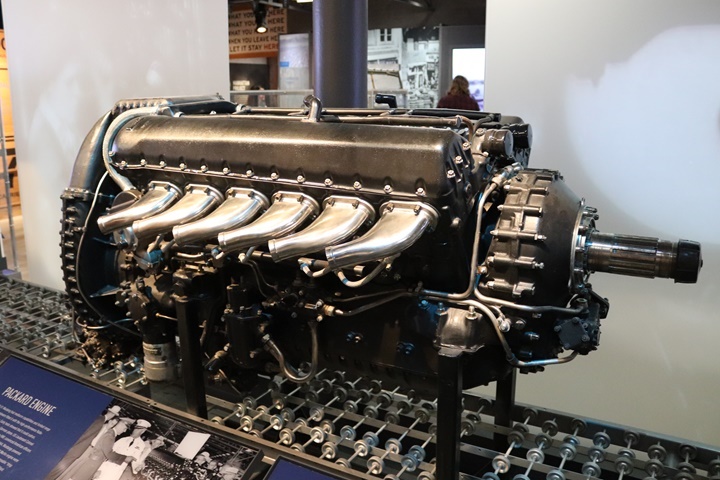
This is a Packard-built Rolls-Royce Merlin
V-1650 aircraft engine. Delco-Remy's Bedford plant produced
castings for this engine. There may not have been much publicity
for this within the General Motors organization, as this was a direct
competitor to the Allison V-1710. The Merlin was also a better
engine than the Allison, which was no doubt an embarrassment to Allison
and General Motors. Author's photo added 5-8-2020.
Kings Mill, OH:
On April 28, 1944 it was announced that the U.S. Navy had taken control
of the former Kings Mill Army Ordnance plant in Kings Mill, OH, and that
Delco-Remy would build cranking motors for diesel powered landing craft.
By the end of the war, in just a year's time, the plant had produced
64,000 naval cranking motors and 375,000 switches. This was done
with a work force of 900 employees.
Before Delco-Remy took over management of the plant, Remington
Arms produced ammunition in it until March of 1944. The .30
carbine ammunition being made in the plant could not be produced in the
quantities needed and was moved to a larger plant. Then the U.S.
Navy took control from the U.S. Army. Delco-Remy tooled up the plant in 60 days for the
production of naval cranking motors and switches for landing craft.
Currently, the former location of
the plant is contained within the grounds of an Army Reserve Center.
|